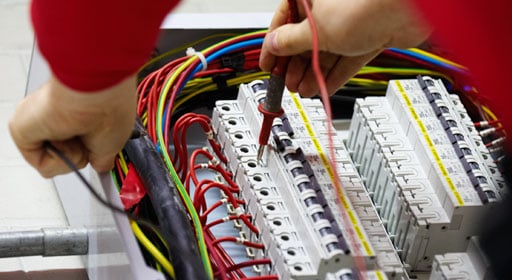
Live Testing or Live working shall be defined as the practice of working on parts of the electrical system while the part in question is still live. This may or may not include the removal of covers or protective devices without isolating the means of supply during such an operation. The safest way to conduct electrical work is to shut off electric power and work on de-energized equipment. However, there may arise extraordinary circumstances that necessitate work on energized equipment. Live testing helps ensure all electrical apparatuses within the circuit are set within their respective recommended electrical polarities for continuous flow of electrical energy.
What is Done During Live Testing?
Live testing applies to all electrical conductors and equipment operating at 50 volts nominal, or greater. This procedure also applies to live parts operating at less than 50 volts nominal, if there is an increased risk of exposure to electrical burns or to explosion due to electrical arcs.
Live working may not be undertaken unless the following applies (as prescribed by “The Electricity at Work Regulations” regulation 14):
- It is unreasonable in all circumstances for it to be dead.
- It is reasonable in all circumstances for him to be at work on or near it while it is live.
- Suitable precautions (including where necessary the provision of suitable protective equipment) are taken to prevent injury.
- The use of all insulated tools and matting and protective equipment in use. Situations where working “live” is acceptable.
Live working may be undertaken only when adequate precautions are taken to prevent danger or injury to all persons:
- Persons carrying out work on live equipment shall be competent to do so safely.
- Live exposed parts shall not be left unattended at any time.
- Live work will only be carried out where there exists no risk of water ingress to live exposed parts.
- Live work may only be carried out where it is impracticable to isolate the supply.
- Signs shall be fitted in all cases on circuits under test stating “Warning, circuit under test “Do Not Operate”.
Situations where working “live” is unacceptable:
The following situations are not appropriate to be worked on live:
- Motor terminal covers must not be removed live.
- Panel covers must not be removed if adequate knowledge of that panel is not known.
- Covers shall not be removed in wet environments.
- Live work must not be undertaken where by “risk assessment” danger or injury may occur to the engineer or others.
- Signs shall be fitted in all cases on circuits under test stating “Warning, circuit under test “Do Not Operate”.
Procedures to be implemented when working “live”:
- All suitable precautions shall be taken to prevent “danger” arising.
- All personnel not directly involved with the task in hand will be kept clear of the area at all times.
- Suitable barriers and warning signs shall be erected as and when appropriate.
- If any doubts regarding safety arise then work must be halted and the circuit made dead prior to any further progress being made.
- Precautions shall be taken to ensure that no nearby dead circuits become unexpectedly live.”
- The appointed site representative shall be kept fully informed of areas where live work is being undertaken.
- Signs shall be fitted in all cases on circuits under test stating “Warning, circuit under test “Do Not Operate”.
How to Conduct Live Testing?
Following are the tests that we carry out during live testing:
Polarity Testing
We require a polarity test to ensure that all single pole devices (fuses, switches and circuit breakers) are connected in the PHASE conductor only. We cannot simply trust that the electrician(s) have connected things up the right way; everyone makes mistakes, even if it’s your own work. “Basically it is a test that creates a circuit using the phase conductor and the single pole device in question, breaking the circuit when operating the device, means that the reading on the instrument will change, and thus confirming that that device must be connected in the phase conductor.
It ensures apparatus connected to the circuit is connected correctly, and does not become damaged. Plug in tester, and ensure the polarity is correct according to the charts on the test instrument. (Varies from tester to tester)
Earth Loop Impedance Test
The main reason for earth loop impedance testing – which is often simply called loop testing – is to verify that, if a fault occurs in an electrical installation, sufficient current will flow to operate the fuse or circuit breaker protecting the faulty circuit within a predetermined time. i.e.; ensure the resistance of the earth cable is not so high as to prevent it from working correctly in the event of a fault. The objective is to make sure that the circuit is disconnected fast enough to prevent overheating and possibly a fire.
To perform the test plug in the instrument, set the range to the lowest setting first and press test, then record the result.
Three-wire no-trip testing is one of the method used in earth loop impedance testing. It requires connections to be made to the live, neutral and earth conductors, and typically uses a test current of 15 mA or less. Its benefits are that there is no need to bypass RCDs and RCBOs during testing, which saves time, and that it does not trip MCBs. There are, however, a few limitations.
Prospective Short Circuit Test
It helps to ensure that in the event of a short circuit, the cable tested can carry enough fault current, to trip the MCB or blow a fuse, as quickly as possible (and within the stated regulation guideline times of 0.4 seconds for socket outlets (portable equipment) and 5 seconds for fixed equipment). A PSC test calculates the current that will flow in the event of a short circuit fault between the live conductors. That is, Line and Neutral on a single phase installation or Line to Line/ Line to Neutral on a three phase installation. Result should be recorded in hundreds of amps.
Residual Current Device Test
RCD testing is the process of safely “tripping” your RCD to ensure it will operate quickly should there be an electrical incident. This is also known as safety switch testing. Your RCD is designed to trip, or switch off all the power to that circuit. It is done to ensure that the RCDs installed will trip fast enough in the event of a fault, to prevent electrocution.
To do RCD testing plug in test equipment (set at the rating of the RCD), and set the test at 0.5 of the RCD’s rated tripping current – the RCD must not trip out. Repeat the test at the rated tripping current of the RCD, the device should trip out in around 0.3 of a second. Repeat the test again, setting the test at 5 times the rating of the RCD, the RCD must trip faster than the last result (even though only slightly)
To make sure that your facility is safe to use, its advised to ensure that the electric circuit, which is exposed to conditions likely to cause deterioration and consequent danger, and is supplied at a voltage in excess of 125 volts AC, undergoes a periodic check by certified authority like Carelabs, so we can establish the ongoing safety of the electrical equipment. While live testing may be required in order to find the fault, live repair work must not be carried out. The individual circuit or item of equipment must first be isolated.
Carelabs is authorized provider of Electrical Installation’s Study, Analysis, Inspection, and Certification services in UAE, and provide live testing service.