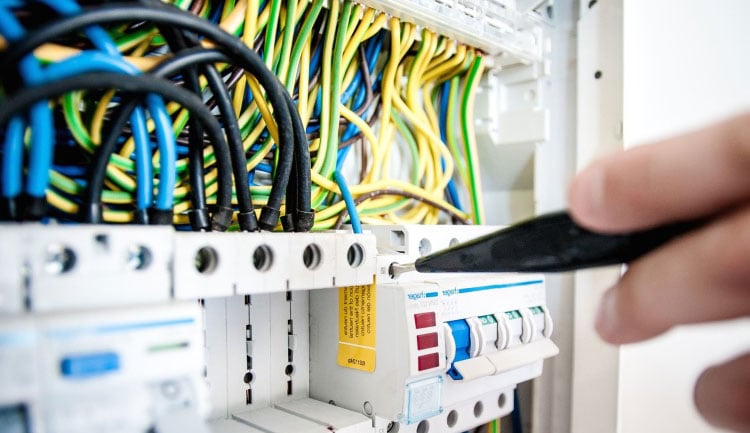
Carelabs is authorized provider of Electrical Installation’s Study, Analysis, Inspection, and Certification services in UAE, and offer electrical safety testing services.
Electrical safety testing and certifying has been carried out by safety agencies for almost a century. Electrical and electronic products have changed dramatically over the years, requiring the safety standards to evolve to accommodate the changes in technology.
Not all consumers and manufacturers fully understand the reasons for and importance of proper electrical safety testing. Shock hazards vary in severity and range from a tingling sensation to a lethal jolt. Identifying, correcting, and eliminating shock hazards are the primary reasons for electrical safety testing.
The equipment used to certify and verify a product’s electrical safety also has changed over time. The technology has improved the work, accuracy, reliability, operator protection, and data capture of test results and critical product knowledge. Advancement to test equipment makes safety testing simpler and more efficient for the manufacturer.
Why Do We Need Electrical Safety Testing?
The obvious answer is consumer and operator protection from shock hazards. Shock hazards exist when a voltage and current are accessible to the operator with respect to earth ground.
According to OSHA’s Publication 3075, a shock hazard considered to exist at an accessible part in a circuit between the part and ground or other accessible parts if the potential is more than 42.4 V peak and the current through a 1,500-Ω load is more than 5 mA.
Studies recognized that the human body can feel an electrical shock with as little as 1.0 mA of current. Since the human body is not a fixed resistance, the voltage required to produce 1.0 mA of current can vary greatly based on the minimal impedance of the human body under various conditions. Some models use a human body resistance value of 1 kΩ to 100 kΩ.
Many types of consumer electronics are battery powered and carry out at safety extra-low voltages which are not considered a shock hazard to the consumer. However, the chargers for these batteries plug into the wall and have the voltage and current to hazard. As a result, they need testing for electrical safety compliance.
Consider your cell phone. Most of the time it presents no shock hazard to you. However, when you plug it into the charger and connect the charger to a wall outlet, you now have a possible shock hazard. If the insulation between the charger and your phone were to fail, the primary voltage applied to the charger could present on conductive surfaces to which you have access.
When Is Electrical Safety Testing Required?
Safety testing required at the point of manufacture, before the product is available to the user. Manufacturers of electrical and electronic products must make sure that no hazardous voltages or currents are accessible to the user. They need to test their products to decide if they meet minimum safety levels.
To analyze this issue, safety agencies, panels of consumer advocates and manufacturers have developed electrical safety standards. These standards make sure that properly designed and constructed products will be electrically safe. They identify types of equipment and the possible shock hazards from each, the minimum requirements for protecting the operator from high voltage and leakage currents, and test methods that decide if the product’s insulation system meets the minimum requirements. There also is the issue of design conformity and liability of the manufacturer.
The manufacturer’s liability rests on conformance. The manufacturer must make sure conformance by testing 100% of the products it produces. Proof of compliance, including records of tests carried out, required complying with safety agency standards.
The manufacturer must manage accurate records to make sure it builds products with the same materials and processes on the same basis. The manufacturer must report the safety agency of any changes to the material, design, or process used in producing its product. If the manufacturer makes a change, safety agencies may amend the safety certification. In some cases, the product may need to rectify.
How Do You Verify and Certify That Your Products Are Safe?
Test equipment manufacturers have created equipment specially designed to carry out the tests as defined in the safety agency standards. These tests include the following:
AC and DC Hipot or Dielectric Withstand Test
A typical hipot tester or dielectric withstand tester will apply an AC or DC high-voltage potential between the input live AC wires and AC ground or the ungrounded metal enclosure. The test passes if the measured current during this test does not exceed the specified maximal allowable current. Usually, electricity set for 5 mA or less, depending on the safety standard you are following.
Leakage Current Test
There are different types of leakage currents. The maximal allowable leakage current for each of these differs based on the associated safety standard. The most critical standard for leakage current is for medical equipment, IEC 60601-1, where leakage defined as:
- Earth Leakage Current: current flowing from the mains part through or across the insulation into the protective earth conductor.
- Enclosure Leakage Current: current flowing from the enclosure or parts, excluding applied parts accessible to the operator or patient in normal use through an external conductive connection other than the protective earth conductor to earth or to another part of the enclosure.
- Patient Leakage Current: current flowing from the applied part via the patient to earth or flowing from the patient via an F-type connector applied part to earth originating from the unintended flow of voltage from an external source on the patient.
Insulation Resistance Test
Insulation resistance test is very similar to hipot testing. In simple terms, it is the applied voltage divided by the measured current resulting in the calculated resistance. It is a method of characterizing the condition of an insulator.
The most common methods by which insulation may degrade environmental such as heat, cold, humidity and contamination. Many of these insulators are subject to heating from soldering during the manufacturing process and cold or high humidity when not properly stored. In addition, physical damage may occur, causing deformity of the insulation material. Since the thickness of the material can affect insulation resistance, it is common for stretching and compression to change the insulator thickness, which changes the insulation’s resistance. Any sharp object, even something as small as metal filings, also may puncture the insulation.
Typically, insulation resistance measured in MΩ. Measuring the insulation resistance during the manufacturing process make sure that the insulation has not been degraded.
Ground Bond Test
Ground bond testing confirms the ground connection from the DUT to the earth ground is adequate to carry two times the current rating of the DUT.
There are further improvements to safety test equipment not defined by the safety standards but based on feedback from manufacturers.
Simultaneous Testing of Ground Bond and Hipot
When manufacturers are producing high volumes of product, even a few seconds saved can equate to improved process times and higher volumes. Simultaneous testing of ground bond and hipot would save the manufacturer process time and money.
Many safety test equipment manufacturers have developed high-voltage and high-current multiplexers to allow multiple products to test from a single safety test device. These are known as scanners and multiplexers, and capacity varies from one or two devices to tens and hundreds of devices.
Corona Discharge/Flashover Detection/Breakdown
All hipot and dielectric test equipment has the ability to corona discharge. Safety agencies have not included any necessities to measure the corona discharge for measuring the electricity leakage dynamically in very small levels. It is possible to decide if the unit is in one of the following conditions:
- Corona Discharge: An electrical discharge brought by ionization of a fluid surrounding. A conductor which arise when the potential angle exceeds a certain value but conditions detect a breakdown, and some can detect flashover, but only a few have the added ability to detect are not enough for a complete electrical breakdown. Corona discharge may consider as an early symptom of an impending breakdown.
- Flashover: Leakage of the gas generating plasma discharges is due to electricity flowing through non-conductor such as air.
- Breakdown: A sudden decrease of resistance of an electrical insulator that can lead to a spark through the insulator. This is a brief event such as ESD lead to a continuous arc discharge if protective devices fail to prevent electricity in a high power circuit.
Open Short Check
It is important to know if the DUT is properly connected to make sure that the hipot test or insulation resistance test has performed. On test equipment manufacturer has developed a method to make sure the connections to the DUT are normal, open or shorted referred to as the open short check.
Based on the fact, any equipment with conductors separated by an insulator would bring capacitance, applying a high frequency, measuring the impedance and then it can decide if the connection is open, shorted or normal.
Ground Fault Interrupt and Operator Protection
Hipot and dielectric withstand test equipment can present an electrical shock hazard to the test operator. Manufacturers have included ground fault circuit to prevent the operator from being electrically shocked.