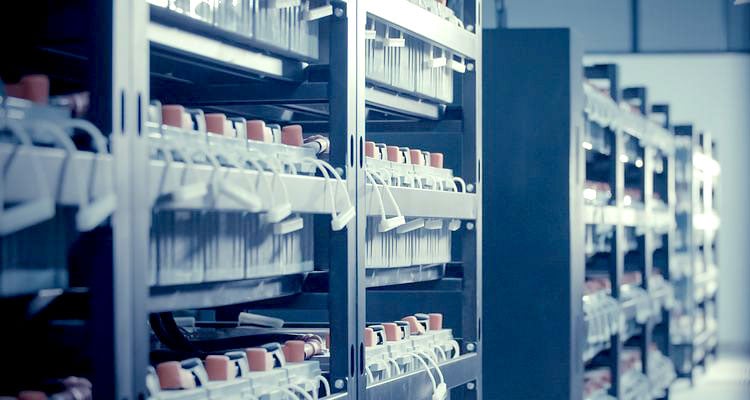
Batteries are used to ensure that critical electrical equipment is always on. There are so many places that batteries are used it is nearly impossible to list them all. Some of the applications for batteries include:
- Electric generating stations and substations for protection and control of switches and relays
- Telephone systems to support phone service, especially emergency services
- Industrial applications for protection and control
- Back up of computers, especially financial data and information
- “Less critical” business information systems
Batteries are used extensively and without them many of the services that we take for granted would fail and cause innumerable problems.
Why Test Battery System?
There are three main reasons to test battery systems.
- To ensure the supported equipment is adequately backed-up.
- To prevent unexpected failures
- To forewarn/predict death
And, there are three basic questions that battery users ask:
- What are the capacity and the condition of the battery now?
- When will it need to be replaced?
- What can be done to improve/ not reduce its life?
Even though there are many applications for batteries, they are installed for only two reasons:
- To protect and support critical equipment during an ac outage
- To protect revenue streams due to the loss of service
Even though a battery is considered only as a source of voltage, it is much more than that. It is obvious that batteries are much more complex than mere voltage sources. There are many parameters to verify the condition of a battery. The Institute of Electrical and Electronics Engineers (IEEE) is responsible for promulgating battery testing practices. These practices are only recommendations; they are required to be followed by battery manufacturers in the event of a warranty claim. They also make good sense to follow in order to get the most from your battery assets.
IEEE Recommended Practices:
IEEE has split stationary battery testing into three groups:
- IEEE 450 for flooded lead-acid
- IEEE 1188 for sealed lead-acid
- IEEE 1106 for nickel-cadmium
How Battery Testing Is Done?
There are various tests for verifying whether the battery is in proper condition or not. Testing is designed to tell us things we want to know about individual cells and batteries. Some typical questions are: Is it fully charged? How much charge is left in the battery? Has there been any deterioration in performance since it was new? How long will it last? Do the safety devices all work?
In all of the following tests, and testing in general, the test conditions must be specified so that repeatable results can be obtained, and meaningful comparisons can be made. This includes factors such as method, temperature, DOD, load and duty cycle.
Qualification Testing
Qualification testing is designed to determine whether a cell or battery is fit for the purpose for which it was intended before it is approved for use in the product. This is particularly important if the cell is to be used in a “mission critical” application. These are comprehensive tests carried out initially on a small number of cells including testing some of them to destruction if necessary. As a second stage, qualification also includes testing finished battery packs before the product is approved for release to the customer. The tests are usually carried out to verify that the cells meet the manufacturer’s specification but they could also be used to test the cells to arbitrary limits set by the applications engineer to determine how long the cells survive under adverse conditions or unusual loads, to determine failure modes or safety factors.
Abuse Testing
The purpose of abuse testing is to verify that the battery is not a danger to the user or to itself either by accidental or deliberate abuse under any conceivable conditions of use. Designing fool proof batteries is ever more difficult because as we know, fools are so ingenious.
Cycle Testing
This is perhaps the most important of the qualification tests. Cells are subjected to repeated charge – discharge cycles to verify that the cells meet or exceed the manufacturer’s claimed cycle life. Cycle life is usually defined as the number of charge – discharge cycles a battery can perform before its nominal capacity falls below 80% of its initial rated capacity. These tests are needed to verify that the battery performance is in line with the end product reliability and lifetime expectations and will not result in excessive guarantee or warranty claims.
Electrical Load Test
Measuring voltage tells only part of the story. A load test should also be performed to accurately determine a battery’s condition. One of the most common ways of conducting a load test is with a carbon pile load tester. Batteries can be tested inside or outside of the vehicle. (This should be done by a qualified technician only. The load is usually designed to be representative of the expected conditions in which the battery may be used .It may be a constant load at the C rate or pulsed loads at higher current rates or in the case of automotive batteries, the load may be designed to simulate a typical driving pattern. Low power testing is usually carried out with resistive loads. For very high power testing with variable loads other techniques may be required.
Thermal Imaging
Thermal imaging is used to check for “hot spots” which would indicate points of high thermal stress in the cell or the battery bank. It is a photographic technique which records the intensity of the infrared radiation emitted by a subject using a special camera. The image on the left is of a lithium ion pouch cell after a prolonged discharge at 4C. In this case the temperature is evenly distributed within the cell and the cell terminals are running cool. These tests can help to identify problems such as overheating, inadequate heat sinking or air flow, undersized current conductors and interference from neighbouring cells or devices. The images can also be used to determine the best location for the temperature sensors used in protection circuits.
Electrical Charging and Discharging Test:
By evaluating a battery’s charge/discharge performance, we may effectively simulate the actual working conditions of the battery. The charge process of a battery typically consists of four stages, including the preliminary charge, constant current charge, topping charge and trickle charge. During the discharge process, high-rate discharge does not tend to continue for long. Therefore, simulation of variable pulse discharge current has emerged as a new tendency for developing novel battery charge/discharge testing systems. What’s more, the simulation must be so flexible that it can satisfy various usage requirements of the user.
Since the main battery will be discharged, an event of an outage during the discharge test. The proper way to discharge test a battery is expensive and second battery needs to be brought in and connected in the from the load bank need to be connected to each cell to measure cell voltages. The load test is run typically for eight hours or longer. Then the battery is recharged for about three days to a full charge. After that the second battery can be removed. The entire process can take four days with overtime and at great expense. The benefit of discharge testing is indeed an accurate measure of the battery’s capacity and is the only proven method of measuring a battery’s capacity.
Ohmic Testing
There are different types of ohmic tests.
- Resistance-Measures only the resistive value of a battery, The battery also has capacitive and inductive values as well.
- Conductance-(Actually Admittance) This is the reciprocal of impedance.
- Impedance Testing-Measures the resistive, capacitive and inductive qualities of the battery.
Impedance testing has a distinct advantage over resistive type testing. When we look at a schematic representation of a battery there are more than just resistive components to that battery. There are also capacitive and inductive characteristics.
AC impedance testing will detect signs of battery aging sooner than purely resistive measurements. Batteries are NOT resisters. Batteries contain both an electrolyte liquid and solid plates. When liquids and solids meet they create a double layer effect. In essence this is a capacitor. As a battery ages the capacitance of the double layer will change well before the resistance of the plates. Resistive testing ignores the capacitive double layer effect.
Ohmic testing is not an absolute test. The measured value is not compared to a standard known good value to determine if the battery is good or bad.(Ohmic testing is NOT a GO/NO GO Test) Ohmic testing is a relative test. The measured value is compared to the previously measured value to see how much it has changed.
Capacity Test
Battery capacity is a measure (typically in Amp-hr) of the charge stored by the battery, and is determined by the mass of active material contained in the battery. To perform a battery load test to see if service or replacement is necessary. First determine the load by retrieving the CCA (Cold Cranking Amps) from the battery case and reducing this number by half. The discharge rate is one half of the batteries cold cranking rating. Apply this load to the battery for 15 seconds. The battery’s voltage must remain above 9.6 volts at 70° F.
Facility managers should be familiar with and follow regulations affecting battery maintenance in order to maintain valid product warranties and avoid unexpected outages. Perhaps more important for a critical facility operator in understanding how best practices can give facility managers added confidence. A proper maintenance program ensures their batteries will support their power generation, transmission and distribution systems, or that their emergency power system is ready when it is needed.
Ensuring proper battery performance and getting the most out of your investment in this critical asset may take more than just periodic test. That Is why monitoring is a critical component of a preventive maintenance program.
Carelabs is authorized provider of Electrical Installation’s Study, Analysis, Inspection, and Certification services in UAE, and offer battery testing and inspection services.