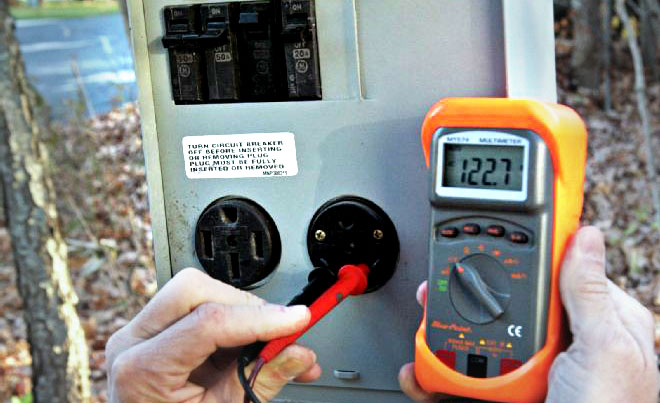
Continuity test verifies that current will flow in an electrical circuit (i.e. that the circuit is continuous). The test is performed by placing a small voltage between 2 or more endpoints of the circuit. The flow of current can be verified qualitatively, by observing a light or buzzer in series with the circuit actuates or quantitatively, using a multimeter to measure the resistance between the endpoint. Carelabs detects the presence of a complete path for current flow.
Continuity testing can be used to detect cold solder connections and problems with wire and cable products. In field applications, handheld multimeters with dual probes are used. Continuity tests can also be used to facilitate reverse engineering. In addition, this form of electrical testing can be used to check connections between the pads and traces on printed circuit boards (PCBs).
Why Continuity Testing is Done?
Regulation 610.1 of BS 7671:2008 IEE Wiring Regulations Seventeenth Edition requires that every installation shall, during erection and on completion before being put into service, be inspected and tested to verify that the requirements of the Regulations have been met. The purpose of this test is to verify that the CPC forms a continuous path around the circuit under test.
A continuity test is an important test in determining the damaged components or broken conductors in a circuit. It can also help in determining if the soldering is good, if the resistance is too high for flow of current or if the electrical wire is broken between two points. A continuity test can also help in verifying or reverse-engineering an electrical circuit or connection.
Continuity testing can be used to detect cold solder connections and problems with wire and cable products. In field applications, hand-held multimeters with dual probes are used. In addition, this form of electrical testing can be used to check connections between the pads and traces on printed circuit boards (PCBs).
What is done During Continuity Testing?
Continuity tester has two leads connected to a small battery, and when you touch the leads together to complete the circuit, the meter should register 0 resistance or if you have a dedicated continuity tester, the light should come on. If you’re using a digital multimeter, the device may also beep.
How to Test for Continuity?
Step 1: The circuit to be tested in the distribution board is selected and the Line conductor from the MCB is removed.
Step 2: Line conductor to the Earth conductor is connected (for simplicity, connect it to one of the spare terminals on the Earth bar). This way we will form a circuit which is half made up of the Line conductor and half made of the Earth conductor (provided that the terminations within the electrical accessories such as wall sockets are correct).
Step 3: Correct test function is selected on the test equipment, which is the low reading ohm meter function (Megger 1553).
Step 4: Next step is to null the test instrument if required (we do this by connecting the two test leads together and pressing the TEST button until the measured value on the display becomes zero ohm`s)
Step 5: Measurement between Line and Earth terminals at each outlet in the circuit is taken. The highest reading is recorded on the Schedule of Test Results as the value of (R1+R2).
Step 6: The Line conductor is returned back in to the MCB.
Continuity of Circuit Protective Conductors (CPC)
The test is carried out as follows:
- The line conductor to the CPC in the Consumer Unit is temporarily link.
- Test between the line and the CPC at each accessory point e.g. a ceiling rose, switch or socket outletis conducted. The reading obtained at each accessory point should be a low resistance value. The resistance measured at the extremity of the circuit is the sum of the resistances of the line conductor and protective conductor (R1 + R2).
Continuity Testing Overview
- Continuity is the presence of a complete path for current flow. A circuit is complete when its switch is closed.
- A digital multimeter’s Continuity Test mode can be used to test switches, fuses, electrical connections, conductors and other components. A good fuse, for example, should have continuity.
- A DMM emits an audible response (a beep) when it detects a complete path.
- The beep, an audible indicator, permits technicians to focus on testing procedures without looking at the multimeter display.
- When testing for continuity, a multimeter beeps based on the resistance of the component being tested. That resistance is determined by the range setting of the multimeter. Examples:
- If the range is set to 400.0 Ω, a multimeter typically beeps if the component has a resistance of 40 Ω or less.
- If the range is set 4.000 kΩ, a multimeter typically beeps if the component has a resistance of 200 Ω or less.
- The lowest range setting should be used when testing circuit components that should have low-resistance value such as electrical connections or switch contacts.
Benefits of Continuity Testing
- Return of that investment is a long-term one and it will also save time.
- Tests can be done 24/7 .
- Fewer human resources are required.
- Reusability: The scripts are reusable. You don’t need new scripts all the time.
- Reliability: It is more reliable and quicker way when running boring repetitive standardized tests which cannot be skipped.
- It not only checks for continuity but also for shorts.