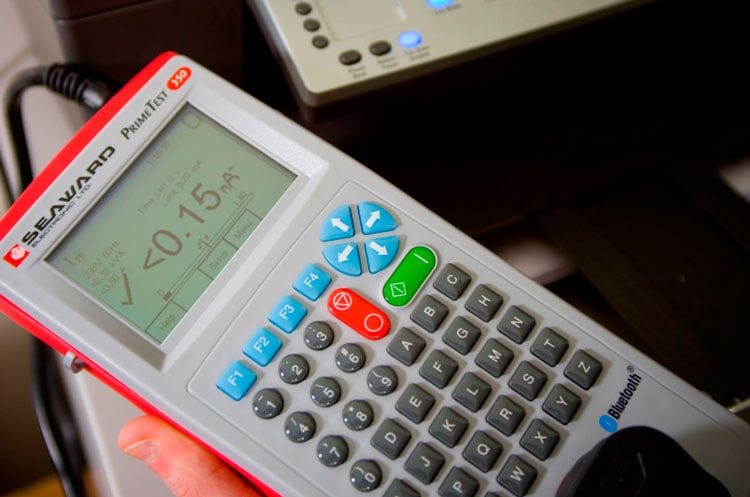
Portable appliance testing (commonly known as “PAT”, “PAT Inspection” or redundantly as “PAT Testing) is the term used to describe the examination of electrical appliances and equipment to ensure they are safe to use. The formal term for the process is “in-service inspection & testing of electrical equipment”. Most electrical safety defects can be found by visual examination but some types of defect can only be found by testing. However, it is essential to understand that visual examination is an essential part of the process because some types of electrical safety defect can’t be detected by testing alone.
The frequency of inspection and testing depends upon the type of equipment and the environment it is used in. For example, a power tool used on a construction site should be examined more frequently than a lamp in a hotel bedroom. For guidance on suggested frequencies of inspection and testing, see: Maintaining portable and transportable electrical equipment.
Why PAT is Done?
The keyword is liability. An employer or manufacturer should show as much concern about safety as does the legal system. The liability is with the employer or owner of a place of business, or public place, to ensure that all electrical equipment accessible by employees or the public is maintained in a safe condition.
There are a number of reasons why appliances should be PAT tested on a regular basis, but we feel the most important ones are:
- To comply with The Electricity at Work Regulations.
- To comply with the Provision and Use of Work Equipment Regulations.
- To minimise the risk of fire and injury caused by electrical appliances.
- To satisfy your Insurance Company.
- To comply with all Health & Safety requirements and ISO standards.
- Quality Assurances also requires you to comply.
Also, one of the first things Fire Officers and Health & Safety Inspectors usually ask to see on any inspection visit is PAT testing records.
What is Done During PAT?
A relatively brief user check (based upon simple training and perhaps assisted by the use of a brief checklist) can be a very useful part of any electrical maintenance regime. However, more formal visual inspection and testing by a competent person may also be required at appropriate intervals, depending upon the type of equipment and the environment in which it is used.
Testing involves a visual inspection of the equipment and any flexible cables for good condition, and also where required, verification of earthing (grounding) continuity, and a test of the soundness of insulation between the current carrying parts, and any exposed metal that may be touched. The formal limits for pass/fail of these electrical tests vary somewhat depending on the category of equipment being tested.
PAT can be done by hiring an external company, like Carelabs, to test all the electrical products in a business or it can be done in-house by a competent person. In a low-risk environment most dangerous defects can be found simply by checking the appliances for obvious signs of damage such as frayed cables.
What Needs to be PAT Tested?
If you have an appliance that has a plug that is intended to be connected to a wall socket or generator, it qualifies as needing to be PAT tested.
This can include items such as electric drills, monitors, printers, PCs, kettles and larger items like photocopiers, vending machines and others. So a cordless power tool would not need to be PAT tested but their battery chargers that plug into the wall for power do need to be tested.
All IT equipment should be tested, including power cords to this equipment although they are required to be tested separately from the equipment that they power, because they are held to a different standard.
Frequency of PAT Testing
In order to determine how often you should have your appliances tested, you should bear in mind a few different factors:
- Equipment that is used more should be tested more frequently. This equipment is likely to suffer less damage than that used regularly.
- If people using equipment report any damages as they become noticeable, there is less chance of a major hazard. If equipment regularly receives damage or abuse that is not reported then inspections and testing are required more frequently.
- The type of equipment in question is a major factor in determining PAT testing frequency. Hand held appliances are more likely to become damaged than those that are stationary. Class 1 appliances carry the greatest risk of danger and should be tested more often.
How PAT Testing is Done?
Visual Examination
Visual examination is vital and always precedes electrical testing. It often reveals major defects that would not be revealed by testing alone.
Categories of in-service visual examination and electrical testing are divided into three types:
- Operator checks (no records if equipment is OK).
- Formal visual examination (recorded).
- Combined visual examination and electrical testing (recorded).
If the cable passes your visual inspection, use a standard test lead (included with most PAT testers) to perform the following testing procedures:
Earth Bond/Continuity Test
Earth bond/continuity tests only apply to Class I equipment and are used to confirm the existence of a safety return path. The purpose of the test is to ensure that the ground terminal has a low resistance connection to the conductive metal casing of the appliance. An effective connection to the system ground within the fixed installation of the premises ensures safety.
Insulation Test
The insulation test is used to confirm that there is separation between the live conductors (live and neutral) and any accessible conductive parts. Generally, insulation testing is carried out by applying a known test voltage (500 V DC) and measuring the resistance. On sensitive equipment (IT for example) 500 V may cause damage, and so be unsuitable. Therefore, it may be substituted with a low-voltage (250 V) insulation test, a touch current test or an alternative leakage current test.
Differential Leakage Test
The differential leakage current (also called protective conductor current) test measures the difference in current between the live and neutral conductors and determines if any current is flowing to earth. Normally, appliances should have no, or very little, earth leakage current. Class II (double insulated) appliances could exhibit earth leakage through their mountings or by operator contact. During the test, the actual mains voltage is measured at the appliance socket. To ensure that the equipment is safe even when the mains supply rises to its maximum permitted value, the PAT calculates and displays the leakage current that would flow at this value.
Leakage current test
It is performed at rated voltage with values not exceeding 5mA for Class I appliances or 1mA for Class II appliances. Alternatively, we measure insulation resistance values are not less than 1MΩ for Class I and Class II appliances at 500 V dc, to avoid the equipment apparently failing the test because the metal oxide varistors (MOVs), or electro-magnetic interference (EMI) suppression has triggered, for equipment containing voltage limiting devices such as MOVs, or EMI suppression, at 250 V dc.
Load Test
The load test (also called the operational or VA test) measures the power consumption of the equipment when running. By setting a load VA limit in the instrument’s test groups, an appliance can be assessed automatically for excessive load. The load VA limit is usually set based on the rating plate on the appliance. When using the Megger portable appliance testers, which power up the equipment for you, a functional test is carried out during the “load” test. This test will determine:
- If the asset functions correctly.
- The VA rating of the appliance.
Polarity Check
In countries where the sockets are polarised, polarity testing is a simple test that can be carried out using a polarity tester to determine whether the active and neutral of the plug end are correctly connected to the corresponding terminals at the socket end.
Flash Testing
Flash testing measures the leakage current when high test voltages are applied to an asset. The flash test provides a high ac test voltage (2500 V or 3000 V) and measures the leakage current. This test can be destructive and is usually only used on equipment that has been repaired. It is not generally used for “in-service testing” of electrical equipment.
Labelling
Any equipment that requires visual examination and electrical testing is clearly labelled. The label must consist of a unique identifier for the equipment, the date it was tested, the re-test date and an indication of its state. A failed asset does not need the dates on, just clear identification that it has failed. Labels are either filled in by hand or printed. Printed labels often consist of a bar code for the identifier making them easy to read with a suitable barcode scanner.
Documentation
The following records are established and maintained:
- A register of all equipment.
- A record of formal and combined visual examinations and electrical tests.
- A register of all faulty equipment.
- A repair register.
Our company maintains the following paper or electronic records: Copy of the formal visual examination and combined visual examination and electrical test results and register of all equipment repaired
Report
On completion of the testing you will be issued with a safety certificate and a detailed report that provides information on each individual item. All items that pass the inspection & testing will be labelled with a safety sticker and a unique barcode number that helps us keep track of all portable appliances in your company. Our reports are done in a way that makes them easily understandable.
Appliances that fail our testing will be labelled with a DANGER DO NOT USE tag, the plug wrapped in red insulation tape, any visible damage highlighted with red insulation tape, the appliance placed in a separate ‘failed’ area, detailed in the certified report, and identified to the appropriate staff member. Our testing remains consistent throughout the country. Carelabs use the same systems and latest test equipment to ensure such consistency.
Carelabs is authorized provider of Electrical Installation’s Study, Analysis, Inspection, and Certification services in UAE, and conduct PAT testing service in UAE.