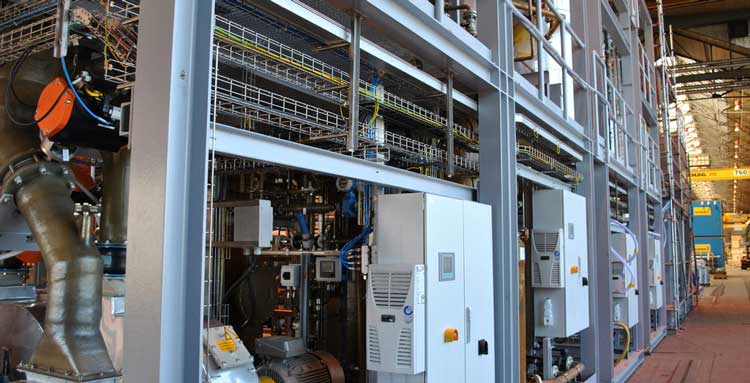
The Factory Acceptance Test (FAT) is a customized testing procedure that evaluates the equipment during and after the assembly process by verifying that it is built and operating in accordance with design specifications. FAT ensures that the components and controls are working properly according to the functionality of the equipment itself. As the name suggests, this testing is performed at the factory.
FAT must be conducted in a thorough and forthright manner. A poor or rushed FAT can lead to missed non conformities, which can only then be corrected after the equipment is installed—which in turn can wreak havoc on a project schedule.
Why use Factory Acceptance Testing Service From Carelabs
FATs are beneficial not just for the buyer and end users but for the manufacturer as well. Both parties can be assured that the equipment meets all the contractual specifications and any issues can be addressed before arriving at the customer’s site.
Our broad factory acceptance test is the most lucrative way to ensure that your equipment or plant operates correctly. As a highly qualified, independent third-party, we have the trusted skills and resources to perform steadfast testing. Alternatively, we can witness appropriate testing on your behalf. In many cases it is difficult to predict the correct operation of the safety instrumented system or consequences due to failures in some parts of the safety instrumented system. For that reason the FAT is a valuable check of the safety issues.
Factory acceptance test helps you to:
- Achieve independent proof of functionality, quality and integrity with our comprehensive checking process.
- Verify all important documents, such as manuals, instructions, plans, drawings, piping and instrumentation diagrams (P&IDs).
- Ensure that your equipment or plant performs as expected under the testable range of likely conditions, including mishandling and error.
What are the Process in Factory Acceptance Testing
The main objective of the FAT is to test the safety instrumented system (logic solver and associated software together). The tests are normally executed during the final part of the design and engineering phase before the final installation at the plant. The FAT is a customized procedure of checking the safety instrumented system and the safety instrumented functions according to the safety requirements specification.
Following are the points to remember while conducting Factory Acceptance Test:
- Provide a detailed test plan.
- Push the envelope, but use the right materials as well.
- Engage the operators and technicians.
- Be smart about training.
- Create and follow a detailed “failure script.”
- Test parts replacement and changeover procedures.
- Take your time.
- Get a good integrator.
- Work with your supplier, and your supplier will work with you.
- Know the difference between a Factory and Site Acceptance Test.
The purpose of the FAT is to verify the desired functionality of the machine. On acceptance of a FAT, you’ll be looking for items such as:
Completed Factory Acceptance Test Protocol
- Maintenance and users’ manuals.
- Easy-to-use training materials (OPLs, videos, etc.).
- Standard work procedures.
- Standard maintenance procedures.
- Recommended spare parts lists.
- Certificates of compliance.
- As-built technical drawings (electrical, mechanical, pneumatic, and process schemes).
- Materials certificates and data sheets.
- Main equipment data sheets.
- Instruments calibration certificates.
- Welding processes qualifications.
How Carelabs Conduct Factory Acceptance Testing?
Before the FAT begins, the manufacturer should present the FAT procedure to the client for review and approval. The procedure should include testing of as much functionality as is practical in the factory and, where possible, should show pass/fail criteria or desired results for each item tested. Once the procedure is approved, the manufacturer should test the equipment before the FAT begins:
Step 1: Process done before Factory Acceptance Test (Pre-FAT)
A pre-planning is necessary for an efficient FAT. The procedures to carry out the FAT shall be well defined and documented in a proper way. Each test procedure shall be described in a logical sequence i.e. How to test the application software and hardware. The needed competence for involved test personnel is described during the planning. It is recommended that personnel with experience suitable for the intended process application and safety instrumented system deals with the FAT planning.
- The testing included in a FAT procedure should be largely derived from the performance criteria defined in the Functional Requirements Document (FRD), which is created by the project team early in the project planning process. The FRD should be the focal point for discussions when interviewing potential system integrators and should be included in the contract/purchase order package. These requirements should, therefore, be well known and understood well before time to develop the actual FAT protocol.
- The system integrator/dealer should prepare and submit a FAT procedure well in advance of the FAT. This procedure should be reviewed and approved by the system owner/project manager. It should attempt to include testing of as much functionality as is practical in the factory, and check of all interfaces among equipment and systems. Where possible the procedure should show pass/fail criteria or desired results for each item.
- The dealer should also provide a schedule for the FAT showing all timing and sequence of testing.
- Prior to FAT all design approvals should be complete. This is to remove technical ambiguity from the FAT and prevent disputes over work that continues after FAT.
- The dealer should prepare a test facility that can be effectively used to conduct the FAT testing, including calibrated test equipment and any special test equipment.
- The dealer should compile a document set that can support the testing and serve as a reference for the test results, including:
- Contract specifications and copies of all references called out in the specification.
- All drawings for the project, including drawings received from other vendors that describe interfaces.
- Detailed testing check list, including pass/fail criteria.
- The dealer is to pretest the system before FAT. Failure to do this can result in wasted time during FAT, and potentially a prolonged extension of FAT while fixes are effected.
- If the system in question is large enough to impact the system owner’s facilities, laboratory layout or utilities or if there are any questions regarding moving the system into the owner’s facility, it is highly recommended that a person responsible for the owner’s physical plant/facility be invited to attend FAT.
Step 2: Process done During Factory Acceptance Test
- We review the specification line by line while checking the equipment or drawings for compliance with the specification, including any change orders.
- We inspect for workmanship.
- Next we inspect for problems that can occur during installation or use of the equipment, for example, lifting points and safe access to components for maintenance, etc.
- We test of the equipment per the dealer’s approved procedure; these should include functionality testing and regulatory testing. Ad hoc testing may be required to define any major non-conformities revealed by testing.
- Next we note the software and firmware versions in the equipment being tested.
Step 3: Processes done After Factory Acceptance Testing
All the test cases of the FAT shall be explained in the documentation and furthermore if the objectives and criteria of the tests have been met or not. Exposed failures during the test are documented and the causes for the failures are also documented supported by essential actions to correct the failures. If there are modifications of the safety instrumented system it is necessary to carry out a safety analysis in order to determine if the safety is affected and if re-testing is necessary.
Benefits of Factory Acceptance Test
- Gain independent proof of functionality, quality and integrity with our comprehensive checking process.
- Verify all-important documents, such as manuals, instructions, plans, drawings, piping and instrumentation diagrams (P&IDs).
- Ensure that your equipment or plant performs as expected under the testable range of foreseeable conditions, including misuse and error.