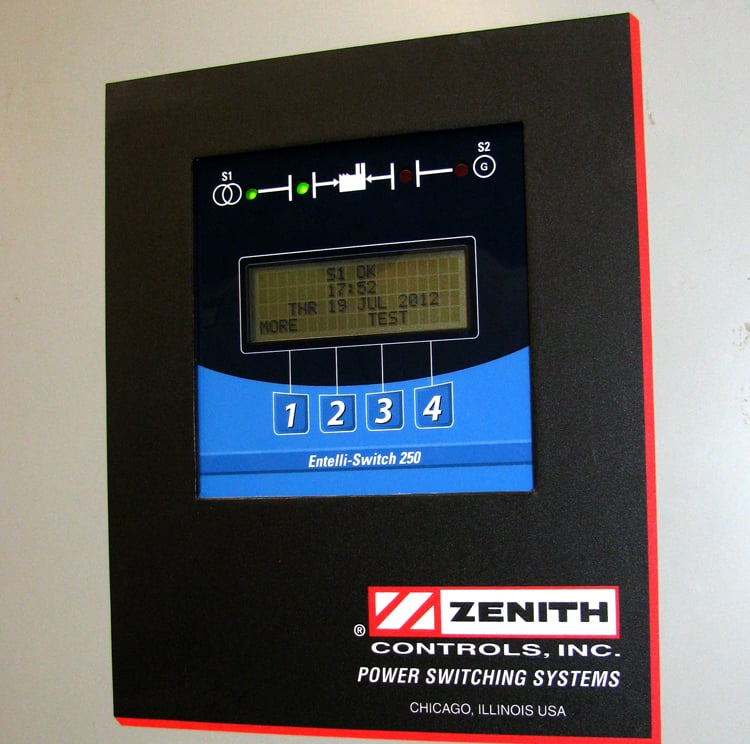
What is Automatic Transfer Switch?
The Automatic Transfer Switch (ATS) is a critical piece of equipment that alternates the origin or the source of power, typically between your utility power and backup/emergency power, ensuring your system’s ability to stay online. It is inherently important in making sure that this part of your emergency system is working properly. Also, because this particular part of your system is usually relatively complicated in nature, they are rarely examined or tested after the ATS has left its manufacturing facility. This is precisely why Industrial Tests, Inc. should be your first choice in ATS testing, so that you and your facility can feel safe and confident in its ability to transfer power, in the event of losing normal power. Automatic Transfer switch tests, tests utility power or standby generator power—and conducts the power to critical loads. The NFPA, Joint Commission on Accreditation of Healthcare Organizations (JCAHO), and all major ATS manufacturers publish literature calling for the monthly test of ATSs, yet many facility owners ignore these guidelines and refuse to perform the tests. There are good reasons for both the monthly-test requirement and for the reluctance of many operators to comply.
NFPA 110, the standard for emergency and standby power supply systems, states “the monthly test of a transfer switch shall consist of electrically operating the transfer switch from the standard position to the alternate position and then a return to the standard position”. The standard also requires a monthly generator run. The best way to perform both these tests is by operating the test toggle on the ATS when the generator isn’t running, and confirming that the ATS properly signals the generator to start and run before transferring building load.
Why Automatic Transfer Switch Testing is Done?
Many critical electrical systems are not being maintained to the proper standard, and some are not maintained at all. Why? Maybe it’s because electrical systems and components are being installed improperly. Maybe it’s because of poor system design that leaves little access. Or maybe it’s because many facility engineers still regard maintenance as a necessary evil. In order to evaluate the cost of maintenance, one must factor in the cost of lost service due to an unplanned failure plus the cost of replacement.
The automatic transfer switch (ATS) is a critical system component of the emergency power system, and proper maintenance of an ATS depends on the type of switch and its position in the critical power infrastructure. It is essential to find out whether your ATS is within manufacturers specifications during a planned examination, so that you don’t run the risk of finding this out during an unforeseen outage and you are unable to switch your system to its secondary power. Intermittent testing of your ATS is the sure-handed method of guaranteeing that your emergency system is as reliable as it can be. Our core group of technicians and engineers have been thoroughly educated and trained on emergency systems, particularly transfer switches. Combining our staff’s training with their vast experience in the field allows for an undeniable recipe for success, where our customers always seek out our expertise and services.
The Three Primary Reasons for the Monthly Test
- A test is an active demonstration that the EPSS is still able to function as intended. If a switch is going to fail to transfer, it’s better to have the switch fail while connected to a live normal source during a test than to have it remain connected to a dead normal source during an actual power outage.
- An automatic transfer switch is an electromechanical device with moving parts. Like the pistons and crankshaft in an automotive engine, the moving parts in an ATS can seize if they’re left in one position for months or years. Regular exercise will help ensure that moving parts will continue to operate smoothly.
- A transfer switch test transfers building load onto the generator for the duration of the generator test. Most standby power generators of more than 100kW are diesel engine driven, and all major diesel generator manufacturers recommend a load of at least 50% of maximum capacity during monthly generator tests. NFPA requires the same thing, for the simple reason that running under a light load is very bad for a diesel engine.
Running a diesel generator in an unloaded condition—with no ATS transfer, thus with no building load connected—causes carbon buildup in the cylinders and exhaust system, a condition known as “wet stacking.” This problem reduces efficiency and power, and in extreme cases it can cause an exhaust system to catch fire. To reduce a wet-stack condition once it has developed, some facility owners will rent a resistive load bank and connect it to the standby generator for a full-load run of sufficient duration to “burn out” the build-up. The cost for such an exercise is substantial, and the relief provided is only temporary.
Reasons Behind the Objection to Testing ATS
Some people mistakenly think that monthly tests will shorten the life of a transfer switch, and are therefore reluctant to conduct them. More often, the reason for refusing to test properly is a fear of the two brief interruptions in power that an ATS test entails. There’s no truth to the idea of a regular test shortening the life of an ATS. Any device to be used as a transfer switch—switching a single electrical load between two sources of power—must comply with UL standard 1008, the only standard applicable to this duty.
Any switch that bears a UL 1008 label can transfer a minimum of 3,000 times, with at least 1,000 of those operations under at least 100% of rated load. (For smaller ampacity switches 6,000 transfers must be under 100% load or greater). A switch that transfers back and forth each month will see 12 transfer operations per year, generally under something less than 100% of rated load. It would take a transfer switch at least 83 years to reach the same level of full-load use that representative switches endure in standard UL testing. And, as mentioned above, a switch that transfers regularly is less prone to seizure than a switch that has remained static for a long period.
The most-cited reason for failing to test transfer switches is that power interruptions can cause problems with lighting, transformers, computers, and other sensitive loads. It’s this fear, primarily, that causes many facility operators to conduct their monthly generator runs without switching building load onto the generator. While problems of this nature can be frightening, they should be no more frightening than the prospect of a transfer switch that fails to operate at a critical time due to lack of testing, or a generator that fails due to wet-stacking.
There are several ways of mitigating or eliminating the problems caused by these power interruptions, both in new construction and in existing facilities:
- For new construction projects the issue of transfer-test-caused interruptions in power is an easy one to solve. The engineer responsible for specifying the electrical equipment should specify “closed transition,” or make-before-break, transfer switches. A transfer switch of this kind transfers when in its test mode, with no interruption in power. Switches of this kind were once a special product available from only one manufacturer, and they carried a daunting price premium. Today, however, closed transition transfer switches (CTTS) are available from several manufacturers, and at a very modest price premium over the old-fashioned open transition switch.
- For existing facilities, a study should be done to determine which specific transfer switches feed loads that would actually suffer any negative impact from monthly interruptions in power. Those loads that are sensitive to interruptions can be protected with UPS systems, or with a timed pre-signal before transfer, allowing for orderly shutdown of the loads before power is interrupted. Also, existing open transition switches can be replaced with CTTS.
Any automatic transfer switch in an emergency or standby power system should be should be tested monthly in accordance with NFPA 110. That test should consist of an automatic generator start, initiated by the transfer switch, followed by an automatic transfer of facility load onto the standby generator. If power interruptions are a matter of concern, closed transition transfer switches should be used to eliminate the problem, or other methods should be used to mitigate the effects.
What is Done During an Automatic Transfer Switch Test?
Following steps are performed
- Simulate loss of normal power.
- Return to normal power.
- Simulate loss of emergency power.
- Simulate all forms of single-phase conditions.
ATS Checks Include
- Check wiring and connections are tight with no discoloration of metal, melted plastic and odour indicating excessive heat.
- Verify external operating mechanism is clean and re lubricate if found dirty.
- Check for any deterioration of wiring insulation such as cuts and abrasions. Replace or repair any damaged wiring.
- Check tightness of wiring connections. Retighten to specification if any loose wiring found.
- Perform insulation resistance tests on all control wiring with respect to ground.
- Perform a contact/pole-resistance test.
- Verify settings and operation of control devices.
- Calibrate and set all relays and timers.
- Verify phase rotation, phasing, and synchronized operation as required by the application. .
- Check ATS main power switching contacts condition. Clean or replace. Replace contractor assembly if necessary.
- Exercise the generator set under load.
- Test the transfer switch’s automatic control system.
- Test all indicators (LEDs) and all remote control systems for operation.
- Inspect the outside of the transfer switch for any indication of wear, excessive vibration, leakage, high temperature, contamination or other deterioration.
- Verify all external components are in place, firm, tightened and not excessively worn.
- Inspect the inside of the transfer switch for any indication of excessive vibration, leakage, high temperature, contamination or any other deterioration.
- Verify all internal components are in place, firm, tightened and not excessively worn.
Standard for ATS Maintenance and Testing
TRANSFER SWITCH MAINTENANCE NFPA 110, Standard for Emergency and Standby Power Systems covers performance requirements for power systems providing an alternate source of electrical power in the event the primary power source fails. This standard includes power sources, transfer equipment, controls, supervisory equipment, and accessory equipment. The standard also addresses installation, maintenance, operation, and testing requirements for these components of the emergency power supply system.
Transfer switches are installed in the emergency power system to transfer the electrical load from the normal power source to the emergency power source (generator) upon failure of normal power. The transfer switch must transfer and retransfer the load automatically. Maintenance programs for transfer switches include checking of connections, inspection or testing for evidence of overheating and excessive contact erosion, removal of dust and dirt, and replacement of contacts when required. The maintenance procedure and frequency should follow those recommended by the manufacturer.
In the absence of manufacturer’s recommendations, NFPA 110 suggests visual inspection and cleaning annually. The 2005 edition of NFPA 110 further recommends an annual maintenance program including one major maintenance and three quarterly inspections. The major maintenance includes a thermographic or temperature scan of the automatic transfer switch. Automatic transfer switches must also be operated monthly. The monthly test consists of electrically operating the transfer switch from the standard position to the alternate position and then a return to the standard position.
How ATS Testing is Done?
ATS is a pretty simple device. It senses power source and behaves according to how it’s set up. Generally it defaults to generator, so with no power all 3 contacts, (30 amp) or 4 contacts, (50 amp) should measure closed and electricity will pass from one contact to the other.
Summarized Procedure for Automatic Transfer Switch Testing and Maintenance
Based on NETA Acceptance & Maintenance Testing Standards, the process includes:
- Contact to pole resistance test.
- Settings and operations verification.
- Control device Examinations.
- Manufacturer’s standards and specifications checks.
- Calibration services.
- Tap connections resistance measurements.
- Verifying engine start sequence.
- Time delay and retransfer functions checks.
- Mechanical parts inspections.
- Anchorage and groundings review for impairment or damage.
- Corresponding parts are properly lubricated and clean of debris or contaminants and more.
Automatic transfers should operate in accordance with manufacturer’s design. For more detail on these tests, see the ATS functional testing procedure described below. A general procedure for functional testing of an automatic transfer switch and standby generator is described below.
Step 1: To begin the test, close the normal source circuit breaker. The switch controller will illuminate the Utility Available LED (if equipped) when correct voltage is sensed. If the ATS mechanism is set on Source 1, the Source 1 position LED will also light. Verify the phase to phase voltages at the utility line terminals.
Step 2: Next, close the Alternate source breaker and start the engine generator. The S2 (Alternate) Available LED will illuminate when correct voltage and frequency levels are sensed. After both sources have been verified, shut down the engine generator, and put the generator’s start control in the automatic position.
Step 3: Simulate a utility outage by opening the Source 1 (normal side) breaker. The delay to engine start timer begins its timing cycle. After the timer has completed its timing cycle, the engine start contacts close to start the generator.
Step 4: When generator voltage and frequency reach the preset restore points the Source 2 Available LED illuminates. Simultaneously, the delay to generator timer begins its timing cycle. When the time delay is completed the ATS will transfer to Generator, the S1 position LED goes off, and the S2 position LED illuminates. Systems shall transfer in no less than 10 seconds where failure of the equipment to perform could result in loss of human life or serious injuries.
Step 5: Reclose the Source 1 breaker to re transfer to the normal source. The delay to utility timer begins its timing cycle. When the timer has completed its timing cycle, the ATS will transfer. The S2 position LED goes off, and the S1 position LED illuminates.
Step 6: The delay engine stop timer will begin its timing cycle. The generator runs unloaded for the duration of this timing cycle. When the timer completes its timing cycle, the generator will stop. The S2 Available LED goes off. A minimum time delay of 5 minutes should be provided for unloaded running of the EPS prior to shutdown to allow for engine cool down (NFPA 110). The minimum 5-minute delay is not required on small air-cooled prime movers 15 kW or less.
Apply a field testing label in accordance with NFPA standards indicating that the transfer switch is electrically and mechanically sound and suitable for service after completing all tests.
Whether you are looking for routine maintenance, or wanting to troubleshoot ATS failure or have emergency systems queries, contact Carelabs at 971 4 514 9730 or +971 55 792 1054 (Call or WhatsApp) or email at [email protected] . We offer monthly, quarterly and semi-annual inspections and testing.