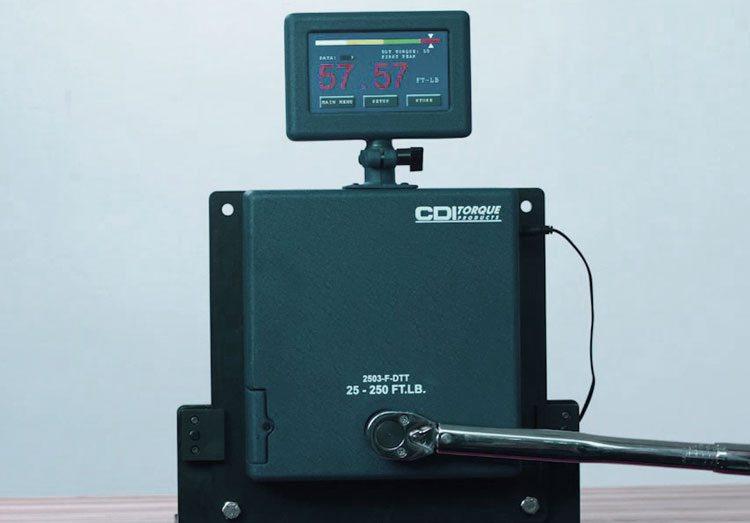
The angular force necessary to rotate something is known as torque. For example, force. Torque is used to create tension in threaded fasteners When the nut and bolt are tightened the two plates are clamped together. The thread converts the applied Torque into tension in the bolt shank. This is turn is converted into a clamping force. The amount of tension created in the bolt is critical.
What happens when you over torque?
The process of over torqueing is one in which you are tightening a nut or bolt head and stretching the bolt. In such cases bolt will get stretched and essentially becomes weaker. It also results in bad connection.
If the torque is too low, the nut could vibrate or become loose.
Bolt torque testing is also known as fastener testing. Two of the more common applications for torque testing are in fastening and in products with rotating parts such as motors, engines or transmissions. By analyzing and measuring the torque characteristics in these applications, the quality of the part or process can be determined precisely along with the main reason for a wide range of defects.
Why Torque Testing is Important?
Most electricians don’t realize that a bolt and nut is not a means for AC Current to flow through. The actual resistance of the bolt is a much higher resistance that the resistance of two sandwiched pieces of copper.
When a bolt is torqued to spec, it firmly applies pressure to the copper, making the resistance lower. Low resistance is good when pertaining to electric. Current flows in the path of least resistance. So, if the copper connection is lower than the bolt, all current will go through the copper and not the bolt. That is the purpose. If it’s over torqued bolt caused the bolt to melt in half while testing.
The National Electrical Code requires that equipment be installed according to its listing and labeling. This requirement includes verifying the given torque setting.
Benefits of Torque Testing
- Loss of energy can be prevented when connections are tight. After all, property owners may be paying premium prices and would want the benefit of each electron instead of losing energy that is dissipated at loose connections.
- Preventing fire hazards is another huge reason to perform torque test. When the conductors are not making good contact, this can create arcing, sparking and overheating, with the result being a fire.
The field assemblies should be fastened using necessary torque gears. The connections that should be torqued in the field normally consist of bolts, connectors and terminals including the following items:
- Breakers
- Neutral/ground bars
- Mechanical, insulated, piercing lug
- Bolts on compression-type connectors
- Mechanical lug & Lay-in lugs
- MSB bussing, bolt-in breakers
Although factory connections in equipment should be tightened to the proper value when they arrive at the job site, there may be indications of loosened connections apparent to the inspector. If connections are loose, they should be tightened again to a suitable torque value.
What is Done During Torque Testing?
When torqueing, not only are we looking for loose connections but there may be some connections that are over tightened and now stripped. A stripped connection is not always evident by visual inspection only. You may notice a skewed setscrew or damaged setscrew on a mechanical lug, which could indicate a stripped connection. When breakers are stripped, there may be no obvious visual sign.
Both loose and overly tightened connections create a risk of failure. Neither industry standards nor equipment manufacturers suggest periodic retightening of connections. Even when a “hot” connection is detected during an infrared inspection, simply tightening the connection probably will not correct the deficiency.1 The connection must be disassembled, cleaned and reassembled with the proper tool and torque. Additionally, cutting off the previously connected end of the wire and making the connection with an unused section of wire is the safest solution.
- 1 inch-pound torque wrench
- Torque screwdriver
- Square drive
- Slotted bits
- Hex socket set
- 1 pair of tongue-and-groove pliers
- Channellocks
- Torque seal
All tools should be calibrated to allow for an accurate torque value. New torque devices come fully calibrated and will stay calibrated for a year. Each year thereafter, recognized companies must calibrate the equipment and apply a sticker showing the date the calibration was done.
Torque values usually are present in the sides of breaker. If that value is absent, which is often the case for older equipment and breakers, default torque values can be found in the 2008 National Electrical Code Handbook (after section 110.14). In the 2011 NEC and newer codes,3, 4 they can be found in Annex I. These values should never be substituted for the manufacturer’s instructions.
How is Torque Testing Performed?
A shortage of measuring and monitoring torque is a shortage of quality control. Insufficient torque can cause a screw or bolt to loosen from vibrations. Excessive torque can cause fasteners to overstretch and break. Once a torque design is found out for a joint, an ideal practice is to carry out periodic audits to make sure correct torque is being attained.
There are 3 methods performed in a torque test sequence:
The Movement Check
In this a wrench that has a torque meter on it is used (Generally, these can be rented or bought cheaply online). Using this technique to find out the torque in an installed fastener includes turning the fastener in a clockwise route, as you would when fastening it. The aim is to attempt to make it move a little, and then record the torque reading when this first happens. It’s vital that you don’t move the fastener too much, mainly if it’s too tight and is within its boundaries. Once the bolt is tightened, use a torque measuring equipment to mark off the workpiece and fastened bolt. Apply extra force in the tightening direction until movement is observed. Recording the reading will indicate the remaining torque applied to the joint in the beginning.
The Loosening Check
Loosening test also called breakaway test operates similar as the movement check except an extra force is employed to the fastened bolt in the loosening direction. At the exact position that the bolt breaks loose, note the reading and mark it off. The amount of torque necessary to loosen the bolt is the torque applied to the bolt in the beginning.
The Marking Check
This method is one-sided, but it’s still valid. After fastening the bolt, mark the bolt surface of the work-piece. Then loosen the bolt. Tighten it again until the markings re-align. The torque necessary to resume the bolt to its initial position is the torque value of the bolt. One of the main plus point of utilizing this test is the fact that it is easy to do. You can utilize it for most kinds of fasteners, even Nylon screws.
Most often a torque wrench is what we will use to test torque.
There are few precautions that should be taken while using torque wrench:
- Select a wrench that reads the desired torque at 50% to 70% of the wrench’s capacity.
- Ratchet extensions do not affect the torque reading, because they do not extend the lever arm.
- Don’t employ a torque wrench that has been stored with the spring set bigger than ten percent of capacity.
- Always “exercise” a torque wrench through its full range of settings before using it.
- Always apply smooth, steady pressure to a torque wrench-do not jerk it.
- When a torque wrench breaks continuing to twist can break the wrench and even cause injury. Thus, stop rotating immediately.
- Do not use a torque wrench for more than an hour without setting it to zero.
- Always store a torque wrench with the spring set at zero.
- Don’t use ia torque wrench in the place of a regular wrench when you don’t need to test torque.
- Always follow the instructions that come with the torque wrench.
- Know the location of a qualified service center to calibrate and lubricate your wrench.
Performing a quality torque testing routine creates a secure domain through exactness and precision. Measuring torque is essential for companies to ensure their product’s quality, safety and reliability isn’t compromised. The failure of a three-cent fastener that isn’t properly tightened can lead to catastrophic or latent failures. Bolts that are not tightened sufficiently can vibrate and extreme torque can strip threaded bolts and nuts.