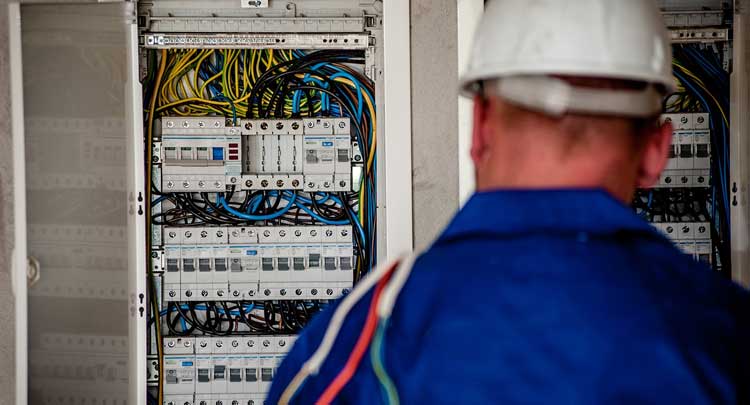
Prospective Short Circuit (PSC) and Prospective Fault Current (PFC) are both designed to calculate the maximum current that will flow within a fault loop path during the event of an electrical fault as required by regulations.
The Prospective Short Circuit Current is the maximum current that could flow between Line and Neutral conductors on a single phase supply or between Line conductors on a three phase supply. A PSC test calculates the current that will flow in the event of a short circuit fault between the live conductors. That is, Line and Neutral on a single phase installation or Line to Line/ Line to Neutral on a three phase installation. A PFC test calculates the maximum current that will flow in the event of an earth fault; i.e., Line to Earth.
The test result can be determined by calculation, ascertained by enquiry to the relevant electricity board, or measured using a Loop Tester. If you are using a Loop Tester, you would measure both PSC and PFC values and record the highest value. Due to the nature of different supply types, you would expect to find a PSC value higher than a PFC value on both TT and TN-S systems, however on a TNC-S system both the PFC and PSC value should be identical.
Why PSC and PFC are Done?
It is important that we conduct the tests to make sure that the protective devices installed within a circuit are rated at the correct breaking capacity. Within a domestic installation, it is common to find 6000A (6kA) rated MCB’s installed within a circuit. If a domestic premises is situated particularly close to a supply sub-station and the measured external impedance (Ze) of the property was 0.03 Ohms, Ohm’s law calculates that 7,666A may flow in the event of a fault on a 230V supply. This may cause concern if the switch gear is only rated at 6000A.
What is done During PFC and PSC Tests?
PSC is determined by the voltage and impedance of the supply system. It is of the order of a few thousand amperes for a standard domestic mains electrical installation, but may be as low as a few milliamperes in a separated extra-low voltage (SELV) system or as high as hundreds of thousands of amps in large industrial power systems.
Protective devices such as circuit breakers and fuses must be selected with an interrupting rating that exceeds the prospective short-circuit current, if they are to safely protect the circuit from a fault. When a large electric current is interrupted an arc forms, and if the breaking capacity of a fuse or circuit breaker is exceeded, it will not extinguish the arc. Current will continue, resulting in damage to equipment, fire or explosion.
PFC is conducted at the origin of the installation, such as at the main switch or at other switchgear connected directly to the tail from the electricity distributor’s metering equipment. Where a measurement is made at a point in the installation other than the origin, such as an item of switchgear fed by a distribution circuit, it would not be the maximum value for the installation.
Particular care should be exercised during the testing process, as fault conditions are most severe at the origin of an installation, where this test is performed. The earthing conductor, main protective bonding conductors and circuit protective conductors should all be connected as for normal operation during these tests, because the presence of these and any other parallel paths to earth may reduce the impedance of the earth fault loop and so increase the level of prospective fault current.
PSC will be higher than the PFC. Prospective fault current and short circuit current of a circuit is automatically calculated when making a loop impedance test. The calculation uses a nominal circuit voltage, not the actual circuit voltage.
How is PSC and PFC Performed?
The nominal supply voltage used in the calculation is automatically selected depending on the actual circuit voltage. The instrument uses the following voltage values:
Actual measured voltage | Nominal voltage |
< 75 V | 55 V |
≥= 75 V and <150 V | 110 V |
≥= 150 V and <300 V | 230 V |
≥=300 V | 400 V |
The Prospective Short Circuit Current Test Sequence
Step 1:
Prospective Fault Current tester or the PFC function of a multifunctional tester such as the Megger 1553 is selected, and we make sure that the supply is ON, but the Main Switch is in OFF position.
Step 2:
The test leads are connected on the incoming side of the Main Switch, one test lead on Line and another on the Neutral terminals of the Main Switch.
Step 3:
TEST switch is pressed and a note of the value (kA) is made.
For three phase installations each phase is tested separately and the measured reading (test between Line 1 and Neutral, then Line 2 and Neutral and last Line 3 and Neutral) is doubled.
Some test meters require that the third (usually green) lead to be connected on the Neutral during this test. Please refer to the test meter manufacturer’s instruction.
There are two methods for measuring the value of PSC, but these can only be used when the supply has already been connected. By then, the fuses and circuit breakers will already be installed.
- The first method is to measure the impedance of the supply by determining its voltage regulation, that is, the amount by which the voltage falls with an increase in current. For example, consider an installation with a no-load terminal voltage of 240 V. If, when a current of 40 A flows, the voltage falls to 238 V, the volt drop will be due to the impedance of the supply.
- A second measurement method is to use a loop impedance tester see connected to phase and neutral (instead of phase and earth) to measure supply impedance. This can then be used with the supply voltage as above to calculate PSC. Some manufacturers modify their earth-loop testers so that this connection is made by selecting ‘PSC’ with a switch. The instrument measures supply voltage, and calculates, then displays, PSC.
A possible difficulty in measuring PSC, and thus being able to use fuses or circuit breakers with a lower breaking capacity than that suggested by the Supply Company, is that the supply may be reinforced. More load may result in extra or different transformers and cables being installed, which may reduce supply impedance and increase PSC.
In terms of PFC, there is no such thing as acceptable PFC. It is what it is. When testing on 3-phase supplies the simplest and quickest way is to take the highest PFC reading off the single phase and double the value. Use Ohms Law to check. Fault current readings should be very high. Anyway its result must be lower than breaking capacity of the protective device. For example, a BS 1361 type 1 cartridge fuse has a rating of approximately 16.5KA. The result must be lower than this at the origin of installation.
Benefits of PSC and PFC tests
- They give accurate results as its live testing.
- The testing is simple and not much calculations are needed.
- Increased safety for employees and third parties.
- Reduced Insurance Premiums.
- Asset Data management and tracking systems.
- Minor repairs of equipment made onsite to minimise down time.