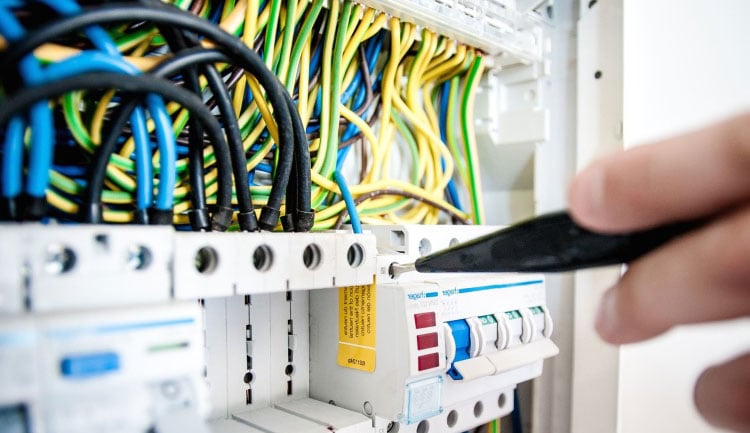
Making a product “safe” requires an understanding of the “hazards” that exist in each electrical product. Certain potential hazards are inborn in all electrical products because of the manner in which they are powered and how they perform their intended functions. Even though a product requires an electrical power source and uses electrical or electronic components, it should not present an electrical shock hazard to the user.
Four fundamental hazards must be evaluated as part of any product safety evaluation:
- Electrical shock
- Mechanical/physical injury
- Low voltage/high energy
- Fire
Although additional safety requirements are also included in most safety standards, these four hazards are the foundation upon which all safety standards are based.
Electrical shock and its effects can be caused and influenced by several factors. The primary effect is the result of electrical current passing through the human body. Severity of the injury to the human body is directly affected by such variables as: the nature of the electrical voltage (AC vs. DC); the pathway through the human body; conductivity of the contact (wet or dry); the size and shape of the individual involved i.e., the person’s impedance), duration of the contact, and the size of the contact area. All these affect the magnitude of current that flows through the person’s body.
Most safety standards address the shock issue by incorporating requirements that instructs appropriate product enclosures: connectors that do not allow direct user access, good dielectric or insulating barriers, as well as very low leakage current. Not all voltage potentials, however, are considered hazardous. Some are considered safe for user contact because of the low levels at which they operate. Since the standards are very specific about these limits, manufacturers must be careful to test their products against the right product standard to be sure that the products are safe.
Why Electrical Safety Testing is Done?
Testing electrical and electronic products for electrical safety is intended to identify the potential risk of electrical shock to users. It is a statutory obligation in most cases. If your premises are open to the public, i.e. pubs, schools, cinemas, clubs, churches, dentists, doctors etc. then you most likely need to be inspected yearly. If you are a private dwelling then you should be tested at least every 10 years.
Electrical testing is often overlooked by ignorance, many companies now delegate the responsibility to dedicated companies. Carelabs keeps a data base of all tests and the results, when they are performed. This way there will be clarity.
Electrical Testing is Important!!
Carelabs conducts electrical testing of the fixed equipment (cables, sockets, lights, etc.) and PAT (Portable Appliance Testing) simply put if it has a plug on it, it will and has to be tested. This is a requirement for all types of installation, Industrial, Commercial and Domestic. Home-owners wishing to sell their dwelling can use our same service to make the test results available to potential purchase.
Electrical safety is mandatory for legal access to every major country in the world. It can help prevent unsafe products from reaching the market, reducing the number of deaths and injuries, as well as costly product recalls and potential litigation. Manufacturers whose products that have been tested and certified to applicable electrical safety standards send a clear signal to buyers and the general public of their commitment to user safety. This question is many manufacturers want to ask, surely the general answer is “because it is regulated in safety standard”.
Both Producer and designer should do their duty to protect consumer safety on safety protection of special product. Passing safety verification doesn’t mean the danger won’t occur. The designers should browse safety related information on usual days, new standard announcement and new test method will effect on test basis of related product.
Electric shock:
Electrical shock is caused by flow of current through human body. This kind of electrical shock has direct effect on human body, the seriousness of injuries depends on degree of electrical energy, humidity, and time duration of the conduction. Shock hazards vary in severity and range from a tingling sensation to a lethal jolt. Identifying, correcting, and eliminating shock hazards are the primary reasons for electrical safety testing.
Electrical shock includes the following four kinds of test:
- Dielectric Withstand / Hipot Test: Withstand test apply high voltage on power and ground terminal circuit of product to measure its collapse status.
- Isolation Resistance Test: Measure product electrical isolation status.
- Leakage Current Test: Inspects whether leakage current of AC/DC power flows to ground terminal is over standard.
- Protective Ground: Inspect whether metal mechanics of accessible part surely grounding.
These tests will be discussed in detail in the following content.
Consider your laptop. Most of the time it presents no shock hazard to you. However, when you plug it into the charger and connect the charger to a wall outlet, you now have a possibility for a shock hazard. If the insulation between the charger and your laptop were to fail, the primary voltage applied to the charger could be present on conductive surfaces to which you have access.
We perform the following equipment checks during visual and physical inspection of all equipment:
- Check for obvious damage or defects in the accessories, connectors, plugs or extension outlet sockets; and for discoloration that may indicate exposure to heat, chemicals or moisture.
Note: For low-voltage portable equipment and cord extension sets fitted with AS/NZS 3112 type (flat pin) plugs and extension sockets, the use of clear backed or integrally moulded (non re-wireable) plugs, and cord extension sockets is recommended. Clear backed plugs and sockets facilitate the easy inspection of the effectiveness of the sheath grip. - Check that flexible cords are effectively anchored to equipment, plugs and cord extension sockets.
Note: This inspection, including flexing and straining at points of entry and clamping points by the application of reasonable combination of push/pull and rotary movements, may detect broken strands or loose connections. - Check for damage to flexible cords that:
- The inner cores of flexible supply cords are not exposed or twisted.
- The external sheaths are not cut, abraded, twisted, or damaged to such an extent that the insulation of the inner cores is visible.
- Unprotected conductors or the use of banding insulation tape are not in evidence.
Note: Carefully running the supply cord through the hand will often detect internal damage such as twisted conductors or broken core filling. Connecting the plugs/sockets of extension leads together helps to confirm that the terminals have not spread. - For portable outlet devices (power boards), check that the warning indicating the maximum load to be connected to the device is intact and legible.
- Check that any operating controls are in good working order – that they are secure, aligned and appropriately identified.
- Check that covers, guards, and the like are secured in the manner intended by the manufacturer or supplier.
- Check that ventilation inlets and exhausts are unobstructed.
How do We Conduct Electrical Safety Testing?
IEC 60335 is the most widely applied standard for electrical safety testing, especially for domestic appliances. Many safety testing standards in the world have been based on it. Electric safety testing will help
- Find any potential electric shock risks and fire hazards.
- Identify any defective electrical work.
- Highlight any lack of earthing or bonding.
- Tests are also carried out on wiring and fixed electrical equipment to check that they are safe.
Following are the basic tests we conduct during electrical safety testing:
High Voltage Test (HiPot test/Dielectric voltage-withstand test)
High voltage test also known as HiPot test or dielectric voltage-withstand test is a non-destructive test that determines the adequacy of electrical insulation for the normally occurring over voltage transient. This is a high-voltage test that is applied to all devices for a specific time in order to ensure that the insulation is not marginal. Hipot tests are helpful in finding nicked or crushed insulation, stray wire strands or braided shielding, conductive or corrosive contaminants around the conductors, terminal spacing problems, and tolerance errors in cables. It guarantees no current flows from one point to another point.
HiPot test is opposite of continuity test. Continuity Test checks surety of current flows easily from one point to another point while Hipot Test checks surety of current would not flow from one point to another point (and turn up the voltage really high just to make sure no current will flow).
Hipot testers usually connect one side of the supply to safety. The other side of the supply is connected to the conductor being tested. With the supply connected like this there are two places a given conductor can be connected: high voltage or ground. When you have more than two contacts to be hipot tested you connect one contact to high voltage and connect all other contacts to ground.
Testing a contact in this fashion makes sure it is isolated from all other contacts. If the insulation between the two is adequate, then the application of a large voltage difference between the two conductors separated by the insulator would result in the flow of a very small current. Although this small current is acceptable, no breakdown of either the air insulation or the solid insulation should take place. Therefore, the current of interest is the current that is the result of a partial discharge or breakdown, rather than the current due to capacitive coupling
Steps to be followed during HiPot tests are:
- Only electrically qualified workers may perform this testing.
- Open circuit breakers or switches to isolate the circuit or Cable that will be hi-pot tested.
- Confirm that all equipment or Cable that is not to be tested is isolated from the circuit under test.
- The limited approach boundary for this hi-pot procedure at 1000 volts is 5 ft. (1.53m) so place barriers around the terminations of cables and equipment under test to prevent unqualified persons from crossing this boundary.
- Connect the ground lead of the HIPOT Tester to a suitable building ground or grounding electrode conductor. Attach the high voltage lead to one of the isolated circuit phase conductors.
- Switch on the HIPOT Tester. Set the meter to 1000 Volts or pre decide DC Voltage. Push the “Test” button on the meter and after one minute observe the resistance reading. Record the reading for reference.
- At the end of one minute test, switch the HIPOT Tester from the high potential test mode to the voltage measuring mode to confirm that the circuit phase conductor and voltage of HIPOT Tester are now reading zero volts.
- Repeat this test procedure for all circuit phase conductors testing each phase to ground and each phase to each phase.
- When testing is completed disconnect the HIPOT Tester from the circuits under test and confirm that the circuits are clear to be re-connected and re-energized.
- To PASS the unit or Cable under Test must be exposed to a minimum Stress of pre decide Voltage for 1 minute without any Indication of Breakdown. For Equipment with total area less than 0.1 m2, the insulation resistance shall not be less than 400 MΩ. For Equipment with total area larger than 0.1 m2 the measured insulation resistance times the area of the module shall not be less than 40 MΩ⋅m2.
Ground Protection Test
Ground protection consists of two kinds of test method:
- Ground Continuity test (GC) and
- Ground Bond test (GB)
The purpose of ground protection test is for protecting users from electrical hazards from touching equipment when unsuitable current is created and flows to the earth. The test method of ground continuity is inputting 1 ampere DC current to power terminal for confirming the resistance value between two ends is lower than 1Ω. Ground bond test is to inputting 25A or 1.5 times rated current to power terminal and check resistance values are lower than 100mΩ.
This test will ascertain whether the earth continuity between the earth supply to the equipment and the internal component earth connections and the metal casing of the equipment are earthed correctly.
- Electrically isolate power supply at fused spur switch and remove fuse. (Always ensure the boiler is fused at 3 amps on completion of work).
- Set Multimeter on ohms scale for resistance readings.
- First put black lead from Multimeter to the retaining screws of the fused socket connection and then the red lead from the multi meter to the boiler casing.
The resistance reading must be no more than 1 ohm and whenever the resistance reading proves to be more than 1 ohm, there is a fault present and must be traced and rectified before proceeding any further. Check all the earth wires for continuity and check all connections are secure.
Poor grounding not only increases the risk of equipment failure; it is dangerous. Facilities need to have adequately grounded electrical systems so in the event of a lightning strike, or utility overvoltage, current will find a safe path to earth.
Simple grounding systems consist of a single ground electrode driven into the ground. The use of a single ground electrode is the most common form of grounding and can be found outside your home or place of business. Complex grounding systems consist of multiple ground rods; connected mesh or grid networks; ground plates; and ground loops. These systems are typically installed at power generating substations, central offices, and cell tower sites.
Warning: Poor earth continuity or no earth continuity at all will create a dangerous situation, as any metal parts that should be earthed may become live and a short circuit may cause an electric shock
Insulation Resistance Test
Insulation resistance test is non-destructive test and can detect if insulation is good. In some regulation, do insulation resistance test firstly then withstand test. When insulation resistance test fails usually withstand voltage test also fails.
The standard insulation resistance test is divided into four steps:
- Charge
- DWELL
- Test
- Discharge
This is the simplest of the tests. After the required connections are made, you apply the test voltage for a period of one min. (The one-min interval is an industry practice that allows everyone to take the reading at the same time. In this way, comparison of readings will be of value because, although taken by different people, the test methods are consistent.) During this interval, the resistance should drop or remain relatively steady. Larger insulation systems will show a steady decrease, while smaller systems will remain steady because the capacitive and absorption currents drop to zero faster on smaller insulation systems. After one min, read and record the resistance value.
The Insulation Resistance Test consists in measuring the Insulation resistance of a device under test, while phase and neutral are short circuited together. The measured resistance has to be higher than the indicated limit from the international standards. The measured resistance indicates the condition of the insulation between two conductive parts. An infinite resistance would be the perfect result, but no insulator is perfect, so the higher the reading the better. To perform the tests needed, you will need an Insulation Resistance Tester or a multifunctional tester such as Megger.
You can use it as:
- A quality control measure at the time a piece of electrical equipment is produced.
- An installation requirement to help ensure specifications are met and to verify proper hook-up.
- A periodic preventive maintenance task, and
- A troubleshooting tool.
Obviously, it’s a good idea to have a basic familiarity with the item you’re testing. Basically, you should know what is supposed to be insulated from what. The equipment you’re testing will determine how you hook up your meghommeter.
When performing insulation resistance testing, you must maintain consistency. Why? Because electrical insulation will exhibit dynamic behavior during the course of your test; whether the dielectric is “good” or “bad.” To evaluate a number of test results on the same piece of equipment, you have to conduct the test the same way and under the relatively same environmental parameters, each and every time. Your resistance measurement readings will also change with time. This is because electrical insulation materials exhibit capacitance and will charge during the course of the test. This can be somewhat frustrating to a novice. However, it becomes a useful tool to a seasoned technician.
Leakage Current Test
Leakage current is the current that flows from either AC or DC circuit in an equipment to the chassis, or to the ground, and can be either from the input or the output. If the equipment is not properly grounded, the current flows through other paths such as the human body. The difference between leakage current test, withstanding voltage test and grounding protection test is the process of testing an equipment under running status. Whatever be the national standard regulation or region standard regulation, the standard of leakage current is different depending on the insulation types of products. “CLASSI, II, III” (which derived from IEC system) A brief descriptions is given below:
- CLASS I indicates anti-shock protection of product not only depends on basic insulation but also includes grounding method.
- CLASS II indicates anti-shock protection of product not only depends on basic insulation but also includes additional precaution. For example double or reinforce insulation but without grounding or installation condition for relying precaution.
- CLASS III indicates anti-shock protection of product depends on power voltage is safety extra-low voltage (SELV) and it don’t generate danger voltage.
Leakage Current Test or a line voltage leakage current test simulates the effect of a person touching exposed metal parts of a product and detects whether or not the leakage current that would flow through the person’s body remains below a safe level. A person typically perceives current flow through his body when it reaches or exceeds 1mA (one thousandth of an ampere). Current above the threshold can cause an uncontrolled muscular spasm or shock. The leakage current is measured by applying a fixed voltage and measuring the voltage across the shunt that is a result of the leakage current. The reference design uses different switchable shunt resistances, which are switched on in a sequence to measure the insulation resistance. When there is a dead short, the insulation resistance is 0 Ω and a full current (or maximum) can pass through the insulation resistance. At this point in the measurement having a smaller shunt value (by turning on all of the switches) is mandatory. In the other case, when the insulation is higher, a higher shunt value is required. The leakage current flowing through the shunt or shunts is measured using a current shunt monitor
How to Select the Correct Safety Test Equipment
The first step to select safety test equipment is to realize your basic requirement, it may be the safety standard your company product need to accord. The test is for promoting product function requirement and consideration of cost and efficiency.
Since hipot tests are usually required for 100% of the units in a production line, and since hipot tests are more stringent, line voltage leakage tests are normally specified as design or type tests and not as production line tests.
Benefits of Electrical Safety Testing
Business Interruptions:
The more power your facility uses, the greater the risk of a failure. Electrical failures are inevitable without preventive maintenance.
Life/Safety Risks:
Electrical distribution system malfunctions are now the leading cause of office structure and basic industry fire in the North America. DON’T RISK IT! Let us help!
Utility Costs:
Without Preventive Maintenance the Electrical Distribution System itself can waste on average $1,000 to $4,000 in Electric Utility Cost annually! We can help to identify and eliminate these wasted costs!
Surge Suppression:
80% of all transients are generated internally by starting and stopping of elevators, motors, heating and air conditioning equipment and manufacturing equipment. Electrical transients, which are spikes of current and/or voltage in a circuit, cause degradation in equipment which commonly get mistaken for manufacturer quality and equipment age. We can help develop a surge suppression plan to ensure the maximum possible protection of your assets.
Power Quality Analysis:
Power quality problems cause loss of data and malfunction of computerized equipment. We can identify and help you eliminate these problems.
Insurance/Certification:
Insurance companies lose millions of dollars each year due to electrical failure. When insurance companies lose so do their customers. More and more insurance companies are encouraging their customers to participate in electrical preventive maintenance. It’s a savings for all.
Asset Management:
The average life expectancy of your Electrical Distribution System is only 15 years when electrical preventive maintenance does not exist. When your electrical system is cared for its life expectancy goes to an average of 30 years. We can help you plan for large upgrades, and avoid emergency repairs.