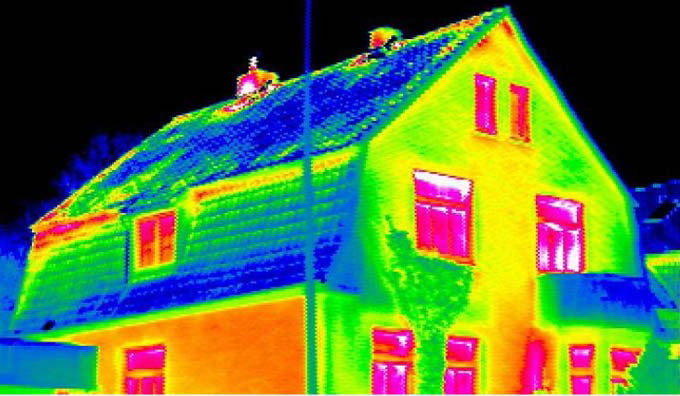
Carelabs is authorized provider of Electrical Installation’s Study, Analysis, Inspection, and Certification services in UAE, and offer electrical thermography services in UAE.
Building envelope thermography inspection was never correctly applied in building inspections, until recently due to the lack of proper training and scientific protocols. During the late 70s and early 80s, a time when fuel prices rose dramatically, thermography was embraced widely as a tool to help determine building performance. The ability to professionally test and evaluate the performance of a building’s envelope is quickly becoming essential for the proper management of today’s commercial and institutional structures.
Several Factors that Necessitate Building Envelope Inspection
- Proliferating government regulations
- New construction techniques and materials
- Rising energy costs
- Growing concerns about occupant health, and escalating litigation
- Moisture damage, frozen pipes,
- High heating costs
Infrared thermography is the only proven non-destructive method for identifying moisture and energy loss. Discovering deficient areas within your facilities, reduce operating costs, and create more efficient building maintenance practices and reduce greenhouse emissions.
An appreciable amount of money can be saved by building owners & operators through the correct application and use of Infrared Thermography Building Envelope Inspections. Timely investment in an Infrared Building Envelope Performance Survey can ensure the structural integrity and safety of commercial or industrial buildings. It can also serve as a quality control tool, to ensure that insulation has been installed correctly.
Building envelope inspection is done at:
- Homes because it instantly shows where your heat loss is occurring in a detailed visual image to assist in achieving a comfortable living environment and reduce energy costs.
- Commercial buildings because Some client specifications of buildings over 500M2 request infrared thermography in order to assess their building integrity alongside an air permeability test.
How is Building Envelope Infrared Thermography Inspection done?
Heat losses from buildings are accelerated by structural problems, poor construction practices, missing or inadequate insulation, moisture infiltration and air leakage.
Thermography measures surface temperatures by using infrared video and still cameras. These equipments see light that is in the heat spectrum. Images on the video record the temperature variations of the building’s skin, ranging from white for warm regions to black for cooler areas. The resulting images help us determine whether insulation is needed or not. They also serve as a quality control tool, to ensure that insulation has been installed correctly.
A thermographic inspection is either an interior or exterior survey. The energy auditor decides which method would give the best results under certain weather conditions. Interior scans are more common, because warm air escaping from a building does not always move through the walls in a straight line. Heat loss detected in one area of the outside wall might originate at some other location on the inside of the wall.
Following are the deficiencies that can be found in a building envelope thermography inspection.
Moisture Intrusion or Condensation
Virtually all of the thermal envelope deficiencies identified by thermographic testing involve the conduction of heat through building materials or the penetration and emanation of air through gaps in the building envelope. Conduction problems are often caused by leakage of exterior water into the building envelope, failure of piping systems, and condensation of moisture vapour within the structure. Moisture considerably reduces the R-value of building materials, resulting in a dramatic increase in the conduction of heat through moisture-damaged components. Other typical causes of conduction losses through the envelope include missing or improperly installed insulation and unintended thermal bridging of structural components.
Exterior Insulation and Finishing Systems
The growing popularity of buildings using Exterior Insulation and Finish Systems has been accompanied by numerous cases of moisture-related structural damage. Water intrudes where sealing have begun to fail. Moisture is then trapped under the skin. Thermography is an invaluable tool to locate moisture in EIFS systems. Inspections are best conducted in the early evening from the outside after a sunny day with little or no wind.
Subsurface Heat Sources
Heating coils are being used more and more either to keep outside walkways or entrance ramps snow free or to provide heat to areas and rooms via hot water or electric cables. Thermography provides a quick way to verify location and performance of these subsurface devices. Typically the thermal pattern shows up very clearly even when the heat source is embedded in several inches of concrete. Similarly, water pipes in wall sections can usually be located quite readily.
Verification of Construction Detail
Thermography is being used with great success to verify bond beams and placement of reinforcing in concrete masonry unit walls. The solid portions of the wall change temperature more slowly than the rest. The inspection can be conducted anytime the wall is in a thermally transient condition, typically in the early evening as it cools down. Because the inspection is conducted during construction, deficiencies can be rectified prior to occupation with relatively minor inconvenience
Roof Moisture Inspections
The inspection of flat roofs, especially built-up roofs has been proven for a number of years. The technique allows for the detection of moisture trapped in a roof system. Over the time this moisture leads to the pre-mature degradation of the roof. The moisture appears warmer at night after a sunny day due to its greater thermal capacitance.
Types of Building Thermographic Inspection Devices
The energy auditor may use one of several types of infrared sensing devices in an on-site inspection
- A spot radiometer (point radiometer):
It measures radiation one spot at a time, with a simple meter reading showing the temperature of a given spot. The auditor pans the area with the device and notes the differences in temperature.
- Thermal line scanner :
It shows radiant temperature viewed along a line. The thermogram shows the line scan superimposed over a picture of the panned area. This process shows temperature variations along the line.
- Thermal imaging camera:
It produces a 2-dimensional thermal picture of an area showing heat leakage. Spot radiometers and thermal line scanners do not provide the necessary detail for a complete home energy assessment.
Qualification of a Thermographer for Building Envelope Thermographic Inspection
Building envelope thermography inspection requires qualified personnel with related experience. Both training and experience are essential. An intimate knowledge of construction techniques, practices, materials, and failures is also important. It is also not unusual for the thermographer to work with other building scientists who have expertise in other areas. Failure to conduct an inspection in a professional manner can result in serious damage to the building and to the occupants.