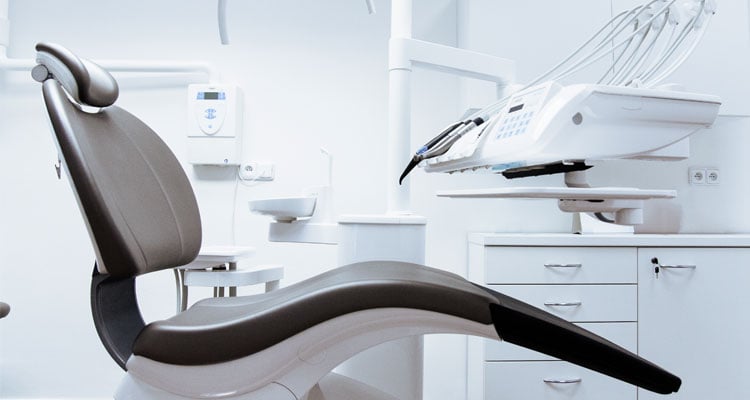
Biomedical equipment (armamentarium) are equipment designed to aid in the diagnosis, monitoring or treatment of medical conditions. Achievements of biomedical equipment installation are significant improvement of health care in all medical specialties, reducing the number of seriously ill people, reduction of mortality. Biomedical equipment technology is used for diagnostic Imaging, radiographic and Fluoroscopic X-ray, diagnostic ultrasound, mammography physiological monitoring, and dental related procedures.
But unintended consequences occur due to causes like improper handling, insufficient or improper staff practice in handling with instruments, insufficient experience, like medical staff rarely read manuals for the users and equipment malfunctions.
Why do we Need Biomedical Equipment Safety Testing?
Biomedical Equipment Safety Testing helps in minimising unnecessary risk to the reputation of your practice and to protect it from litigation or non-compliance. It also helps to maintain practice accreditation and comply with guidelines and standards for medical equipment. To make sure correct readings on medical devices which is important for accurate diagnosis testing should be performed. It also ensures patient and user safety at all times by safety testing of all electrical and electro-medical devices. It helps to safe guard against infection risk to your patients by properly maintaining your autoclave ensuring it is working as it should be. It makes sure to protect your valuable vaccines and practice reputation by ensuring your medical refrigeration is performing correctly all the time and to comply with regulations, electrical safety testing is mandatory.
The facility’s commitment to quality is vital, regardless of the type of company or product that is being manufactured. Periodical testing and repair is not only an excellent routine but shows that there is a system in place in the event of trial. With Carelabs’s orderly, measurable, and appreciable methods we will assist your project and avoid the probability of equipment-related risks, reduce accidents and events, stay consistent with regulatory reporting requirements and limit equipment & supply costs. Carelabs performs biomedical inspection according to manufacturer’s requirement and regulatory agencies.
Services Carelabz Provide in Biomedical Equipment Safety Testing?
When it comes to electrical compliance at all “Patient Areas” such as medical and dental practices. Few areas where Carelabs perform biomedical equipment safety inspection are:
- Doctors consulting room
- Chiropractic and physiotherapy treatment rooms
- Dental surgeries
- CT rooms
- Treatment rooms
- Ultrasound rooms
- Blood collection areas
- X-ray rooms
- Nursing
Carelabs performs whole inspection of medical facility in strict compliance with current laws and regulations using equipment and techniques approved by regulatory agencies.
An effective biomedical equipment inspection programme consists of adequate planning, management and implementation. Planning considers the financial, physical and human resources required to adequately implement the inspection. Once the programme has been defined, financial, personnel and operational aspects are continually examined and managed to ensure the programme continues uninterrupted and improves as necessary. Ultimately, proper implementation of the programme is key to ensuring optimal equipment functionality.
One important aspect of an inspection is to identify defective product, non-conforming product and system failures. The way in which companies investigate and correct objectionable conditions and deficient manufacturing and control systems is an important part of an inspection and typically illustrates the level of quality within a facility.
How do we Conduct Biomedical Equipment Safety Testing?
Biomedical Instrument Safety Testing Include:
Visual Inspection
Visual inspection is a relatively easy procedure to make sure that the medical equipment in use still conforms to the specifications as released by the manufacturer and has not suffered from any external damage or contamination.
These include following inspections:
- Housing Enclosure – Look for damage, cracks etc.
- Contamination – Look for obstruction of moving parts, connector pins etc.
- Cabling (supply, Applied Parts) – Look for cuts, wrong connections etc.
- Fuse rating – check correct values after replacement.
- Markings and Labelling – check the integrity of safety markings.
- Integrity of mechanical parts – check for an obstructions.
Earthbond Test
- Earth Leakage: current flowing down the protective Earth conductor of the mains inlet lead.
- Enclosure Leakage: current flowing to Earth through a person by touching the medical equipment / system or part of.
- Applied Part or Patient Leakage: current flowing through a person to Earth from the Applied Part or current flowing from a person to Earth via the Applied Part by applying unintended voltage from an external source.
Earth Leakage Test
The Earth Leakage Test shows the current flowing through or via the insulation of the Medical Device into the protective Earth conductor.
Enclosure Leakage Test
Enclosure Leakage displays the current that would flow if a person came into contact with the housing (or any accessible part not intended for treatment or care) of the medical device.
Patient Leakage Current
It is the current flowing from the joined part to Earth by means of the patient or streaming from the patient through an applied part to earth, which begins from an accidental voltage appearing on an external source.
Documentation
The record for each device should include identifying data such as a brief description, manufacturer, model, serial number, and location. These data are typically contained in work order records that provide documentation of every task performed on the device. As a result, the inventory database will contain the entire technical history for each device in the inventory.
Benefits of Biomedical Equipment Safety Inspection and Testing
It helps in:
- Prolong the lifecycle of your equipment.
- Protecting your patients, staff and assets.
- Approval agencies and insurance companies may insist on safety inspections & testing.
- Quality Assurance.
- Asset management.