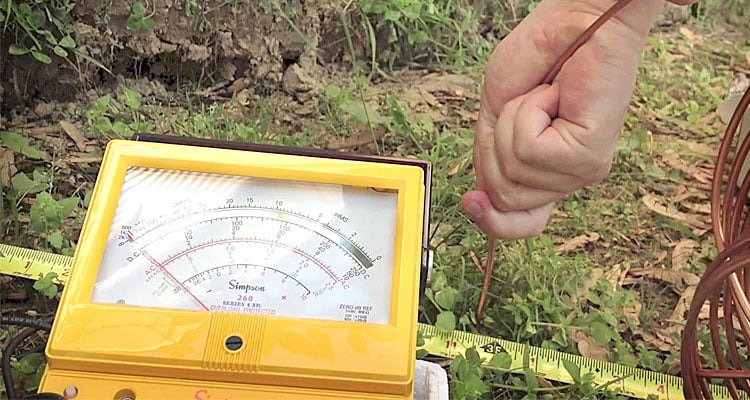
A ground fault is any short circuit that outcomes in an unintentional connection amid a ground and energized ungrounded phase conductor and ground. Ground faults are the most common type of fault on power distribution systems. They are due to the insulation failure or accidental grounding of an ungrounded phase conductor that causes the ungrounded phase conductor to meet ground. Unintentional grounding of a phase conductor can occur when a small animal enters a piece of equipment and contacts both an ungrounded phase conductor and the grounded enclosure. They monitor that the current going out any one phase is coming back on another phase or neutral. If current is going out on a phase but is coming back on the ground path a ground fault has occurred. All systems with ground fault protection include:
- Current transformers to identify ground fault current(GFC)
- A relay or logic box to determine tripping current value and time
- An operating mechanism to trip the breaker or switch
Certain systems have a monitor panel indicating system status and a test panel for generating a ground fault signal to test the breaker.
Why Testing Ground Fault Systems is Important?
According to National Electrical Code (NEC) sections 230-95 and 517-17 performance testing is required. Around 16% of ground fault protection systems tested by NETA comprises of components which are not installed properly, damaged components or does not operate properly. Arcing ground faults can seriously damage distribution equipment, causing fires, which damage facilities and endanger personnel. They also cause extended downtime during system repair. Ground fault protection is the initial step of shield. Once installed, ground fault protection systems stand by until needed to protect services and feeders. However, if these systems malfunction when a ground fault occurs, the distribution system and facility will be as damaged as if no systems were installed. Ground fault systems must be fitted correctly and maintained and tested periodically. An arcing ground fault of even small values spoil switchgear before the main service overcurrent protection gets time to operate. A 480V solidly grounded system possess enough voltage to support an arc between 1 phase and a ground, but not adequate current to cause big main breaker or fuse to eradicate the fault rapidly. The result of this is an arc that is like an electric weld, munching huge values of metal during the time the breaker or fuse functions. A correctly installed and functioning ground fault protection system will identify and eradicate the fault in milliseconds, speedy enough to regulate damage to satisfactory levels.
Few Points to Remember
- Complete field acceptance testing as required by the NEC
- Inspect neutral main bonding connection
- Verify proper installation of sensor(s) and grounding connections
- Inject current through the current sensor and verify pickup and timing characteristics of the relay
- Test operation with control voltage supply decreased to 277V as an alternative of 480V
- Verify functioning of exclusive features like zone interlocks
NEC Article 100 defines ground fault protection of equipment as, “A system envisioned to give safety of equipment from harming line to ground fault currents by functioning to bring about a detaching means to open whole ungrounded conductors of the faulted circuit. This protection is offered at current levels smaller than those needed to shield conductors from harm through the functioning of a supply circuit overcurrent device.” Ground-Fault Sensing and Relaying Equipment requires that manufacturers provide information sheets describing system testing instructions. As a minimum, UL requires the following performance testing for manufacturers’ test requirements:
- Have a trained personal examine the ground fault protection system to safeguard that it was fixed properly according to manufacturer’s recommendations. – Verify that the location of sensors and the polarity of their connections are correct.
- Detect system grounding points to ensure that no ground paths occur that would sidestep the sensors.
- Test the ground fault protection system using either a simulated or actual controlled ground fault to determine that the system settings are correct and that the system is operating as intended.
- Record the results of the performance testing on the manufacturer-provided test form.
In addition, NEMA Publication PB 2.2 requires the following for performance testing:
- Manufacturer’s installation and instruction literature should be reviewed and understood prior to performance testing.
- Performance testing should follow manufacturer’s recommendations.
- Performance testing must be regulated to those tests that find out that the ground fault system has been fixed properly and is functional.
What is Done During Testing of Ground Fault System?
There are two test methods for evaluating ground fault protection systems by using simulated fault current or by high-current primary injection. These methods can be applied to ground-fault relay systems, but to test a system with integral ground-fault trip circuit breakers, only the high-current primary injection method can be utilized. If the high-current test does not create necessary tripping, verify control power at fuses, transformers and at relays. The ground fault relay systems can be tested by the simulated fault current testing method plus a detailed visual inspection, if it is suitable to the local inspection agencies. Or else, it will be essential to utilize the high current primary injection test method.
Simulated Fault Current Method
- A simulated fault current is created by a coil round a window type sensor or with the help of a distinct test winding in the sensor.
- A secondary current in the sensor is created, when the monitor panel sends a small current through the test winding, which the relay act in response to as if it were created by a primary current of thousand six hundred amperes.
- In a similar method which can be utilized with any window type sensor providing a ground fault relay, number of twists of wire are covered round the sensor core, like twenty turns of #14 wire.
- A current is passed through the wire to simulate the ground-fault current, which is approximately 125 percent of the pickup setting of the relay divided by the number of turns
- Testing with simulated fault current offers a way of explaining the functioning of the relay, sensor and shunt trip and the sufficiency of the control power supply.
- GFP system must be checked to confirm. that neutral ground points are placed properly with regard to sensors, that sensor polarities are correct when several are connected in parallel, and that conductors which pass through a sensor window all run in the same direction.
- The significance of adding simulated fault current testing with sufficient inspection is highlighted when 1 understands that the first 5 items on the Checklist are problems that cannot be identified by just simulated fault current testing only.
High-Current Primary Injection Method
- The high-current injection test method might be used to test ground fault protection systems with integral ground fault trips on circuit breakers or ground fault relays.
- It is an alternative to simulated fault current testing along with inspection in the case of relays.
- Integral ground fault protection in circuit breakers can be system tested only with the help of high-current injection test method.
- No. TAK-TS2, which is utilized along with AKR-SST/ECS trips can be used to determine the internal electronics of these breakers.
- High-current testing of ground fault protection systems comprises of injecting full-scale current into the equipment phase and neutral conductors to replicate the ground fault current flow under various states.
- The testing gear needed consists of a high-current supply sufficient enough to deliver up to thousands of amperes or more at 2.5V, or similar.
- With the help of smaller ground fault current pickup settings on relays and breakers or switches, the current necessary to trip can be maintained to a minimum, such as 400 or 300 amperes or less.
- If inspection experts needs tests at complete ground fault protection setting, a current supply sufficient enough to deliver thousand two hundred amperes or more may be necessary.
- Connect the current supply and jumpers between the points indicated in the tables accompanying the diagrams.
- Ground fault protection can be supplied for three wires and four wire gear supplied from a solidly grounded four wire supply.
- This is necessary to offer a low-impedance ground fault current return path to the neutral to make sure functioning of the overcurrent device is correct.
How is Ground Fault Test Performed?
Visual and Mechanical Inspection
- Compare nameplate data of equipment with specifications and drawings.
- Inspect the components for damage and errors in polarity or conductor routing:
- Verify that ground connection is made ahead of the neutral disconnect link and on the line side of any ground fault sensor.
- Verify that the neutral sensors relate to correct polarity on both primary and secondary.
- Verify that all phase conductors and the neutral pass through the sensor in the same direction for zero sequence systems.
- Check that grounding conductor does not pass through the 0 sequence sensors.
- Verify that the grounded conductor is solidly grounded.
- Inspect bolted electrical connections for high resistance using one of the following methods:
- Use of low-resistance ohmmeter in accordance with Section 7.14.2.
- Check stiffness of reachable bolted electrical connections by calibrated torque wrench method according to manufacturer’s published data.
- Perform thermographic survey.
- Verify correct operation of all functions of the self-test panel.
- Verify that the control power transformer has adequate capacity for the system.
- Set time-delay and pickup settings according to the settings given in the owner’s specifications. As asked by NFPA, record suitable functional and test sequences.
Electrical Tests
- Perform resistance measurements through bolted connections with a low-resistance ohmmeter, if applicable.
- Measure the system neutral-to-ground insulation resistance with the neutral disconnect link temporarily removed. Replace neutral disconnect link after testing.
- Execute insulation resistance test on whole control wiring in connection with ground. Employed potential should be 500 V dc for 300V rated cable and 1000V dc for 600V rated cable. Test duration shall be one minute. Follow manufacturer’s recommendation, for units that cannot tolerate the applied voltage or units with solid state components.
- Perform the following pickup tests using primary injection:
- Verify that the relay does not operate at 90 percent of the pickup setting.
- Verify pickup is less than 125 percent of setting or 1200 amperes, whichever is smaller.
- Verify right polarities by employing current to each phase neutral current transformer pair, for summation type systems, utilizing phase and neutral current transformers.
This test also applies to molded-case breakers utilizing an external neutral current transformer.
- Relay must function when current direction is constant relative to polarity marks in the 2 current transformers.
- Relay should not function when current course is contrasting to polarity marks in the 2 current transformers.
- Quantify relay time-delay at 140% or greater of pickup.
- Check decreased control voltage tripping ability is 81 percent for dc systems and 56 percent for ac systems.
- Verify blocking capability of zone interlock systems.
Test Values
- Match up bolted connection resistances to values of same connections.
- Bolt-torque levels should be in accordance with Table 100.12 unless otherwise specified by manufacturer.
- Millivolt drop values or Microhm should not cross the high-level limit of the normal range as stated in the manufacturer’s published data. Investigate any values which stray from similar connections by more than fifty percent of the lowest value, if manufacturer’s data is not accessible,
- System neutral to ground insulation should be at least 1.0 megohm.
- Insulation-resistance values for control wiring shall be a minimum of 2.0 megohms.
- Relay timing should be matching with manufacturer’s specifications but must be slower than 1 second at three thousand amperes.