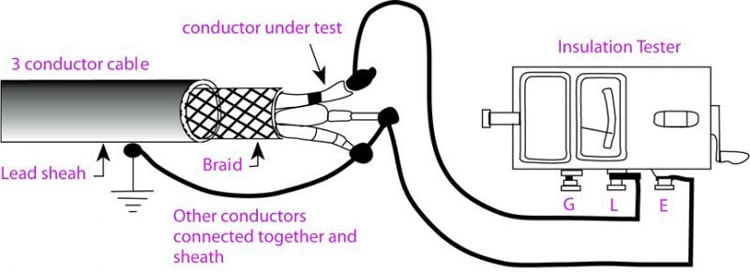
Developed early in the 20th century, the insulation resistance (IR) test is the oldest and most widely used test for assessing the quality of insulation. Insulation Resistance Test is the second test required by the electrical safety testing standards. The Insulation Resistance Test consists in measuring the Insulation resistance of a device under test, while phase and neutral are short circuited together. The measured resistance has to be higher than the indicated limit from the international standards. A megohmmeter (also called insulation resistance tester, teraohmmeter) is used to measure the ohmic value of an insulator under a direct voltage of great stability.
Insulation cannot be perfect in the same way that something cannot be frictionless. This means that there will always be a little bit of current travelling through. This is known as “leakage current”. It’s acceptable with good insulation, but if the insulation deteriorates, leakage can start causing trouble. So what makes “good” insulation? Well, it needs a high resistance to current, and it needs to be able to sustain high resistance for a long time
Why Insulation Resistance Test is Done?
Insulation starts to age as soon as it’s made. As it ages, its insulating performance deteriorates. Any harsh installation environments, especially those with temperature extremes and/or chemical contamination, accelerates this process. This wear and tear can reduce the electrical resistivity of the insulating materials, thus increasing leakage currents that lead to incidents which may be serious in terms of both safety (people and property) and the costs of production stoppages. Thus it’s important to identify this deterioration quickly so that corrective steps can be taken. In addition to the measurements carried out on new and reconditioned equipment during commissioning, regular insulation testing on installations and equipment helps to avoid such incidents through preventive maintenance. These tests detect ageing and premature deterioration of the insulating properties before they reach a level likely to cause the incidents described above.
This test is often used as a customer acceptance test, with minimum insulation resistance per unit length often specified by the customer. The results obtained from IR Test are not intended to be useful in finding localized defects in the insulation as in a true HIPOT test, but rather give information on the quality of the bulk material used as the insulation. Wire and cable manufacturers use the insulation resistance test to track their insulation manufacturing processes, and spot developing problems before process variables drift outside of allowed limit.
Why is a Multimeter Not used for Measuring Insulation Resistance?
Although there is a degree of similarity between a multimeter and megger, the insulation resistance is measured using a Megger (or a similar device), because it’s able to generate a high voltage that creates a moment of stress in the insulation. Insulation resistance is calculated usually in Mega- or Tera-ohms.
In conclusion, a multimeter measures the electrical resistance of a conductor (coil), while a Megger measures the insulation resistance of an isolated group (two coils relative to mass), something that a multimeter is unable to do.
How is Insulation Resistance Measured?
Insulation resistance measurement is done using an IR tester. This is a portable tool that is more or less an ohmmeter with a built in generator that’s used to produce a high DC voltage. The voltage usually measures at least 500V, and causes a current to flow around the surface of the insulation. This gives a reading of the IR in ohms.
Insulation resistance measurement is based on Ohm’s Law. (R=V/I). By injecting a known DC voltage lower than the voltage for dielectric testing and then measuring the current flowing, it is very simple to determine the value of the resistance. In principle, the value of the insulation resistance is very high but not infinite, so by measuring the low current flowing, the megohmmeter indicates the insulation resistance value, providing a result in kW, MW, GW and also TW (on some models). This resistance characterizes the quality of the insulation between two conductors and gives a good indication of the risks of leakage currents flowing.
Well, if we get a high number of IR, you have some good insulation. However, this is not everything – a variety of factors can affect the IR, including temperature and humidity. We will have to do a number of tests over time to make sure the IR value stays more or less the same. Value of insulation resistance is often expressed in gigaohms [GΩ].
A Good Insulation is when megger reading increases first then remain constant. Bad Insulation is when megger reading increases first and then decreases.
Expected IR value gets on Temp. 20 to 30 decree centigrade. If this temperature reduces by 10 degree centigrade, IR values will increased by two times. If above temperature increased by 70 degree centigrade IR values decreases by 700 times.
Types of Insulation Resistance Tests
Short-Time or Spot-Reading Test
In this method, we simply connect the Megger instrument across the insulation to be tested and operate it for a short, specific time period we will simply pick a point on a curve of increasing resistance values; quite often the value would be less for 30 seconds, more for 60 seconds.
If the apparatus we are testing has very small capacitance, such as a short run of house wiring, the spot reading test is all that is necessary. For many years, maintenance professionals have used the one-megohm rule to establish the allowable lower limit for insulation resistance. The rule may be stated: Insulation resistance should be approximately one megohm for each 1,000 volts of operating voltage, with a minimum value of one megohm.
Time-Resistance Method
This method is fairly independent of temperature and often can give us conclusive information without records of past tests. It is based on the absorption effect of good insulation compared to that of moist or contaminated insulation. Tests by this method are sometimes referred to as absorption tests.
This test is of value also because it is independent of equipment size. The increase in resistance for clean and dry insulation occurs in the same manner whether a motor is large or small. We can, therefore, compare several equipment and establish standards for new ones, regardless of their ratings.
Factors Affecting Values of Insulation Resistance
- Capacitance Charging Current: Current that starts out high and drops after the insulation has been charged to full voltage (much like water flow in a garden hose when you first turn on the spigot).
- Absorption Current: Also an initially high current which then drops (for reasons discussed under the section Time-Resistance Method).
- Conduction or Leakage Current: A small essentially steady current both through and over the insulation.
Insulation Resistance should be done to prevent hazards such as electric shock and short-circuits caused when the insulation in electrical devices, parts, and equipment used in industrial plants, buildings, and other settings degrades over long periods of use.