Care Labs provides several services for electrical projects such as electrical safety inspections, electrical system design simulations, power quality study & analysis, power systems study, and analysis. At Care Labs, our team of qualified and experienced professionals carries out comprehensive and thorough electrical safety auditing services.
Our professional team performs audits on electrical installation and the people working on those assets to give our clients the confidence that work is performed to the specifications required.
Need for Electrical Safety Audit:
Electricity is one of the most important resources that we all use every day. But if it’s not maintained properly, it can cause severe injury or even death.
In the past decade, 325 workers died as a result of electrical hazards, which means merely 33 workers per year. So, the risks associated with working on electricity must be assessed, communicated, and controlled.
The safety inspection and testing must be done to the requirements of the Australian/New Zealand standard AS/NZS 3019:2007, AS/NZS 3017:2007 Electrical installations periodic verification, AS/NZS 3760:2010 In-service safety inspection and testing of electrical equipment
The Work Health & Safe -WHS act 2011 regulates that Person Conducting a Business or Undertaking -PCBUs must manage electrical hazard risks at the workplace so they are eliminated or minimized to reasonable limits.
When a PCBU, or senior officer, negligently causes the death of a worker, a maximum penalty of 20 years imprisonment for an individual or AU$10 million for a corporate body applies.
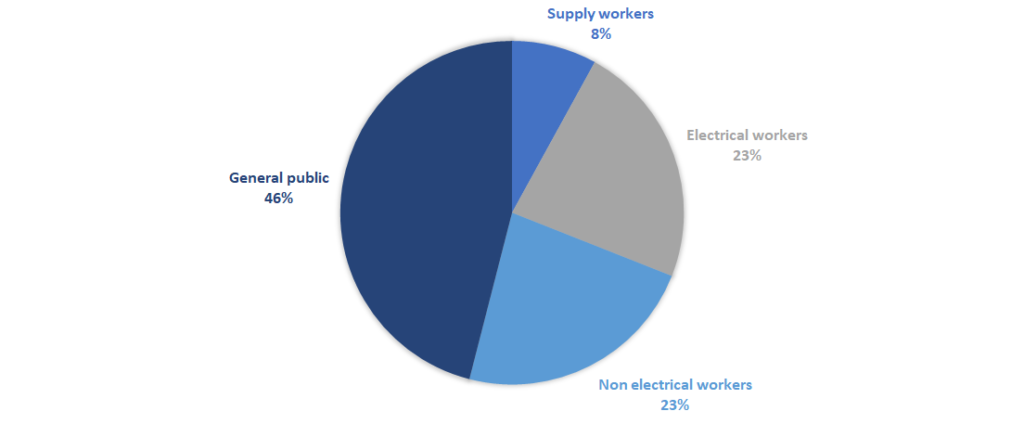
Figure.1: Australia and New Zealand victim categories – 2018-19
To comply with the AS/NZS 3000 standards requirement of all electrical installations and any alterations or additions shall, prior to being placed in service or use, be assessed as far as is practicable.
An Electrical Safety Audit can help in achieving maximum safety standards, minimize injuries to workers and property damage, comply with regulations, and reduced civil and financial losses.
Here are a few reasons why industries should consider Electrical safety check and audits :
- Identifying any flaws in the existing electrical system
- Identification and elimination of safety risk or vulnerability
- Developing a dynamic record of safety performance
- Creation of positive workplace environment of safety improvement
- Improves management awareness of problems
- Ensuring compliance with national and provincial safety regulations and best practices
- Ensuring the longevity of big and expensive electrical equipment
- Training of workers and officials for the safe operation of the facility
- Control actions and measures to be taken for electrical safety
Our Electrical Safety Audit Methodology:
- A Pre-Audit meeting.
- On-site visit and inspection
- Discussion with members of the house.
- Review of documentation / records
- Submission of final electrical safety audit report
What is the Electrical Safety Audit Checklist?
The electrical requirements of any business will vary depending on the kind of work that you do, the type of facility you are in, and the kind of equipment you use.
The electrical requirements vary from business to business, which depends on the kind of your business operation, type of your facility, and the kind of equipment you use.
Electrical safety audits and checklists are also varied from business to business.
A checklist is important to examine a full assessment of your safety performance. It covers various aspects of your electrical safety audit program that must be assessed. It ensures your process is fair and transparent.
Electrical Safety Inspection Checklist Questions:
- Have you established Occupational Health and Safety management system in your facility?
- Have you documented your electrical safety program?
- Have all electrical hazards been identified in the facility?
- Has a risk assessment been performed where required?
- Have employees been consulted in hazard identification, risk assessment, and safety audit program?
- Have employees been trained in safe usage, maintenance operations?
- Any equipment that has left plugged in should be inspected to make sure that they are grounded.
- Check the type of grounding electrodes used.
- Check the size of grounding electrodes and their maintenance condition.
- Check the proper connections and grounding methods for the installations.
Care Labs provides industry-leading specialist services designed to ensure compliance and the safety of the industry and the public.
Care Labs offer electrical safety audit services in all the major cities of Queensland, New South Wales, South Australia, Victoria, Tasmania, and Western Australia.
Care Labs can take care of all your electrical safety with a complimentary electrical safety audit in your facility.