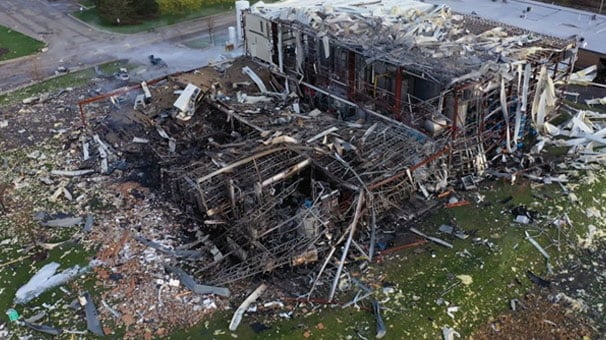
An explosion followed by fire occurred at AB Specialty Silicones in Waukegan, which killed four workers and severely injured the rest. The efforts to recover all the workers from the explosion area took four days, requiring debris, equipment, and structures to be moved under the direction of the Lake County Coroner.
What Happened?
Leakage of hydrogen that went undetected by the facility’s detectors for hydrogen and other flammable gases led to an explosion that resulted in an unknown amount of chemicals being released into the air, causing air pollution and threatening land and water near the facility.
According to OSHA investigators, AB Specialty Silicones failed to ensure that the electrical equipment and installations in the production area of the plant complied with OSHA electrical standards and were approved for hazardous locations.
The company also used forklifts powered by liquid propane to transport volatile flammable liquids, and operated these forklifts in areas where employees handled and processed volatile flammable liquids and gases, creating the potential for ignition.
Analysing the Root Cause:
- Non-functioning detectors for hydrogen or other flammable gases.
- Non-compliance to safety standards
- Human errors in operating procedures
Impact:
- Decimated the entire facility, shook homes, scattered debris for 20 miles and caused almost $1 million in damages.
- Killed four of the nine workers in the building at the time and severely injured the rest
- AB Specialty Silicones faces $1,591,176 in penalties and has been placed the agency’s Severe Violator Enforcement Program
What could have been done to avoid this?
- Use of functional gas leak detector.
- Ensure compliance of electrical equipment as per government laws and policies, standards and international best practices
- Prioritizing leak maintenance followed by regular maintenance of all electric equipment.
- Safety protocols should have been exercised by the management and employees should have been provided with appropriate protective clothing.
What should be done to avoid such incidents in the future:
Having an Electrical Safety Audit (ESA) and Electrical Installation Condition Report (EICR) performed at the site can ensure that electrical systems and appliances within the workplace are safe, suitable for use and maintained suitably appropriately. Part of this involves the inspection and testing of the electrical systems by a competent person, as well as keeping suitable records up to date.
An Electrical Safety Audit is a thorough evaluation of all electrical wiring, connections, and systems for potential electrical hazards, design, and structural flaws. An EICR is an easy and comprehensive means to identify and reduce the risk of expensive electric fires and incidents of electrical origin. An EICR certification also ensures your company fulfills its compliance obligations.
Further, only qualified personnel with the proper training should work on electrical equipment with appropriate electrical safety garments and tools.
Pictures and References:
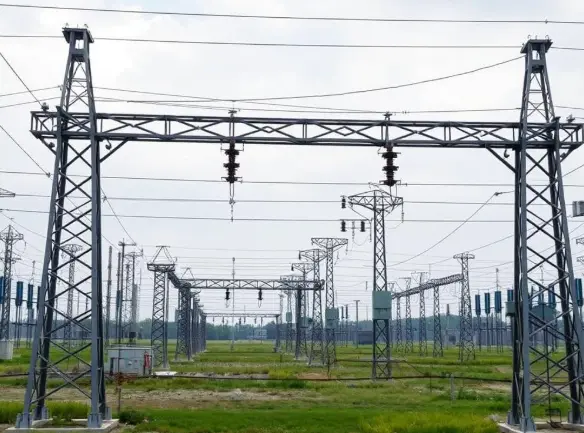
The Importance of Relay Coordination in Power System
Introduction Relays are protective elements that help control faults in a power system. Proper relay coordination helps isolate the fault sections from healthier sections in a power system. Being a fundamental part of ensuring reliability and operational continuity, the strategic configuration of protective relays is imperative in the design of a power system. One way […]

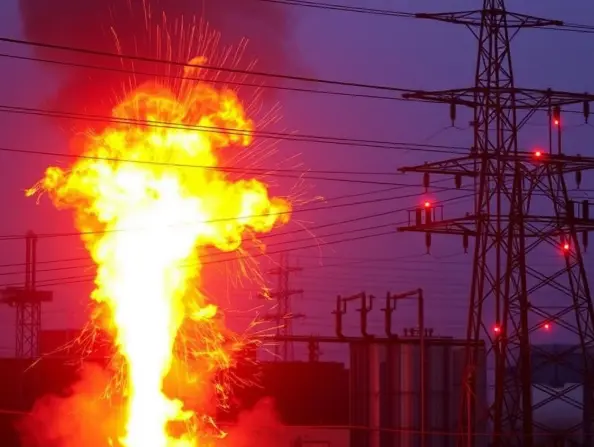
Which of these Facts About Arc Flashes are True?
Introduction In electric hazards, arc flashes are among the most dreadful threats. Despite their criticality, many myths surround arc flashes. Although IEEE and NFPA continuously strive to enhance awareness, five to ten arc flashes happen in the USA daily. We, at Care Labs understand the importance of maintaining a healthy electrical infrastructure. To help companies […]
