Verify
South African Electrical Motor Performance Regulations Compliance:
Industrial electric motors fuel a variety of applications within the global economy. According to the International Energy Agency (IEA), the automotive industry is responsible for up to 70% of all energy used in industrial contexts, 35% of all energy used in the commercial and service sectors, and 45% of all power generated globally. The reality that motor-related delays cost thousands of dollars per hour demonstrates the significance of electric motors in numerous industrial applications.
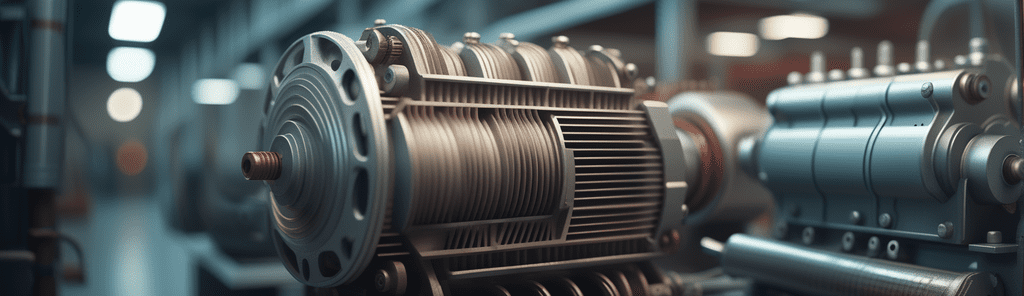
Power facilities are primarily responsible for greenhouse gas emissions and environmental degradation. In addition, they must account for the swiftly increasing electricity demand in developing countries. There is a global economic opportunity to increase the energy efficiency of industrial motors by 20 to 30 percent, with average payback periods of less than three years. Approximately 15%, or 4.3 billion tons, of the world’s annual 26 billion tons of carbon dioxide emissions are attributable to electric generators. Increasing energy efficiency is one of the most cost-effective and risk-free strategies for lowering rising energy demand and greenhouse gas emissions.
Use A Strong Engine for the Following Reasons:
- Reduce operational expenditure
- A more peaceful and tranquil operation
- Enhanced reliability and durability of motors
- Reduced carbon dioxide emissions
Beginning Motor Evaluation:
A portion of the energy that electric motors lose is accounted for by windage and friction losses, as well as losses in the stator, rotor, and magnetic core. These losses may account for the motor’s diminished performance. Considering the energy consumption and industrial applications of electric motors, it is evident that evaluation of efficiency and minimum energy performance standards are necessary and applicable. The accuracy of motor efficiency and motor loss calculations is dependent on the selected test method. There is no distinct method of evaluation utilized across all industries. Despite being a straightforward concept, it may be difficult to measure and validate the energy efficacy of a motor using various criteria.
Methodologies Recognized Internationally for Evaluating Effectiveness:
It is common in industrial applications to discuss the following testing methods:
IEEE 112-2004 is a frequently used test method for polyphase motors and generators. Methods for calculating the efficiency and losses of rotating electrical equipment. JEC 37 was developed by the Japanese Electrotechnical Committee as a standard for induction devices. Standard IEEE 112-2004
This strategy includes ten testing procedures for energy efficiency. To utilize the most vital:
- Simple validation of input and output.
- Verify that both the input and output are lossless.
- Back-to-back test for devices with separation loss that are connected.
- Utilizing normalized residual losses in load loss calculations.
- The Eh-star technique
The IEC standard examination consists of three principal classes:
- Determining a machine’s input-output capacity.
- Measurement of the input-output voltage of two devices back-to-back.
- The losses caused by a single machine were tabulated.
The test procedures for Japanese JEC standard 37 completely disregard the additional load losses. Among the numerous significant economic and environmental benefits of increasing the energy efficiency of equipment and appliances is a reduction in business operating expenses. Our motor start analysis services extend to every significant city in South Africa, including Johannesburg, Cape Town, Durban, and Pretoria.
Related News







Significant Is Harmonic Analysis in South African
Firm?









South African Electrical Motor Performance Regulations Compliance:






How Significant Is Harmonic Analysis in South African Firm?




Why Does South African Business Need Short Circuit and Load Flow Analysis?


