Examine and Confirm Electrical Motor Performance in Compliance with Chilean Regulations
Numerous applications in the global economy are powered by industrial electric motors.
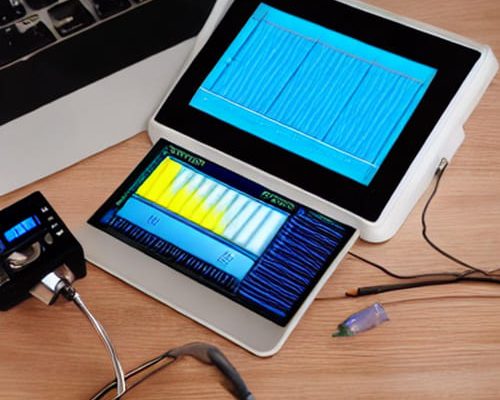
The International Energy Agency (IEA) estimates that the automotive industry is responsible for up to 70% of all energy used in industrial contexts, 35% of all energy used in the commercial and service sectors, and 45% of all power generated globally. The fact that motor-related delay costs thousands of dollars per hour demonstrates the importance of electric motors in a variety of industrial applications. They are primarily responsible for greenhouse gas emissions and environmental damage caused by power plants. They are also to account for the rapidly rising electricity demand in developing nations. There is a global economic opportunity to improve industrial motor energy efficiency by 20 to 30 percent, with average repayment periods of less than three years. Electric generators are responsible for approximately 15%, or 4.3 billion tons, of the world’s annual 26 billion tons of carbon dioxide emissions. Increasing energy efficiency is one of the most cost-effective and risk-free methods to reduce escalating energy demand and greenhouse gas emissions.
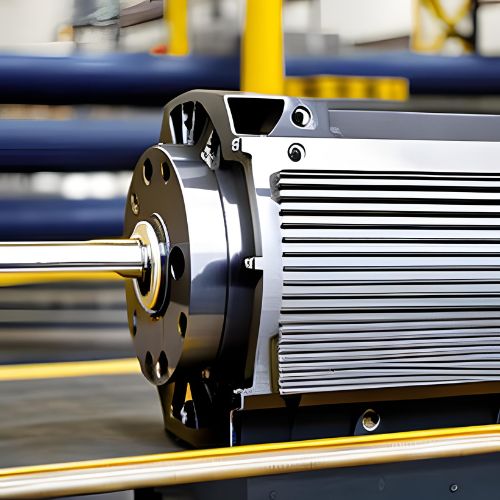
Utilize a Powerful Motor for the Following Reasons:
- Reduce operational costs
- A more tranquil and serene operation
- Increased motor dependability and durability
- Decreased greenhouse gas emissions
Beginning Motor Analysis:
Windage and friction losses, as well as losses in the stator, rotor, and magnetic core, account for a portion of the energy that electric motors lose. These losses may be responsible for the motor’s decreased efficacy. Considering the energy consumption and industrial application of electric motors, it is evident that efficiency evaluation and minimal energy performance standards are necessary and applicable. The accuracy of the calculations for motor efficiency and motor loss is dependent on the chosen test method. There is no distinct assessment method used across all industries. Although it is a simple concept, it may be challenging to measure and validate the motor’s energy efficiency using various criteria.
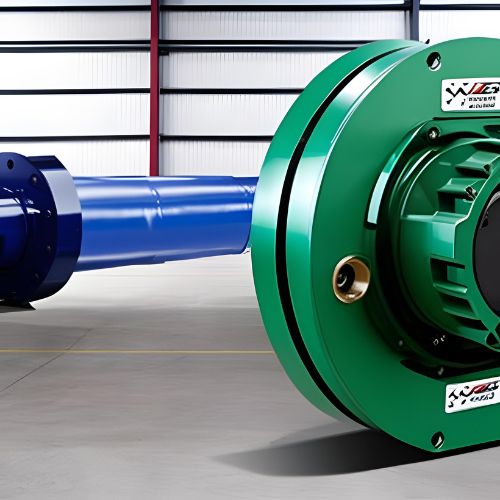
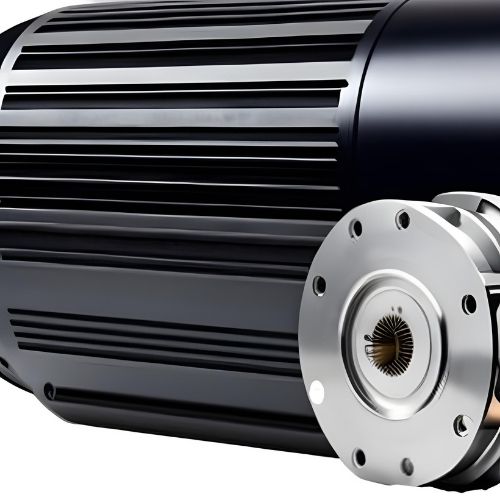
Internationally Recognized Methodologies for Evaluating Effectiveness:
In industrial applications, it is typical to discuss the following testing techniques:
IEEE 112-2004 is a common test technique for polyphase motors and generators. 2014, International Electrotechnical Commission, IEC 60034-2-1, Tests. methods for calculating the efficiency and losses of rotating electrical equipment. The Japanese Electrotechnical Committee created JEC 37 as a standard for induction devices. IEEE Standard 112-2004
This strategy comprises ten energy efficiency testing procedures. To employ the most essential:
- Simple input and output validation.
- Confirm that the input and output are loss-free.
- Back-to-back test for connected machines with separation loss.
- Calculating load losses utilizing normalized residual losses.
- The Eh-star strategy
The IEC standard test encompasses three primary categories:
- Determining the input-output capacity of a machine.
- Back-to-back measurement of the input-output voltage of two devices.
- Losses from a single machine were tallied.
The test procedures for the Japanese JEC standard 37 ignore the additional load losses entirely. Among the numerous significant economic and environmental benefits of increasing the energy efficiency of apparatus and appliances is a reduction in operating costs for businesses. In addition to Santiago, Valparaíso, Concepción, and Viña del Mar, our motor start analysis services cover every major city in Chile.